- Home
- Additive Manufacturing
- 3D Printing Materials
- 3D Printing Material PEBA
PEBA 3D printing solutions
Elastomers have gained large market shares as 3D printing materials, especially in recent years. One reason for this is certainly the possibilities for customizing products with elastic and flexible properties – such as shoe soles.
So today it is possible to perfectly adapt a shoe sole or insole to a person’s running and stress profile. Running comfort, performance improvements and the knowledge of being in possession of a truly unique shoe sole are the results.
Suitable materials for this purpose are thermoplastic elastomers (TPEs): a type of plastic filament that can be deformed when heat is applied and retains its new shape after cooling. This process can also be repeated without the material losing any of its properties. In 3D printing TPE filaments exist alongside TPUs, another type of plastic with similar properties.
Find out more about thermoplastic elastomer (TPE) material for 3D printing. More specifically, discover the high-performance TPE filament, PEBA (polyether block amide) which has a property profile used with 3D printers.
What are elastomers and what is polyether block amide (PEBA)?
Elastomers are plastics that are dimensionally stable but nevertheless elastic and therefore deformable. If they are subjected to a force such as pressure, for example, elastomers absorb the energy and deform, but return to their original shape as soon as the pressure is released. At the molecular level, elastomers consist of a large number of entangled polymer chains that expand in the direction of a mechanical force. This causes the material to stretch or elongate. When the force ceases to act, the polymer chains return to their original entangled form.
Thermoplastic elastomers are of particular interest for 3D printing. They include the material polyether block amide (PEBA). This is a plastic developed by Evonik Industries that is very well suited for powder-based 3D printing due to its high elasticity and strength.
Why are elastomer PEBA filaments suitable for 3D printing?
The properties of PEBA, just like TPU, make it interesting for 3D printing. It exhibits high elasticity and strength, and also shows excellent chemical resistance in 3D-printed form. Since it is a white powder, it can be easily processed with powder-based technologies. 3D printing with PEBA is possible with selective laser sintering (SLS) which can produce very precise and stable components, and high-speed sintering, which also features high precision and high productivity. Find out more about 3D printers for TPEs like PEBA below.
Workshop: HSS poylmer printing
In this workshop we will present our HSS technology in detail: From open source conception to scaling and production possibilities.
Which 3D printing applications can PEBA be used for?
From the sports industry to medical technology and the automotive industry – TPE, mainly PEBA, filaments are used in all of these industries. In the sports industry, PEBA filaments can be used to produce shoe soles, midsoles and insoles using 3D printing. The geometric freedom of 3D printing allows for completely free design. This means that the soles can be adapted to an individual foot profile in a material-saving and function-optimized way by means of topology optimization and lattice structures. Other positive properties of PEBA in this context are its resistance to permanent loads and the fact that PEBA has a very wide temperature window of -40° to 90°C, in which it does not lose any material properties.
In the automotive industry, PEBA is used primarily for the 3D printing of seals or pressure hoses. Here, too, it benefits from its resistance to chemicals and its good impact strength. Medical technology also benefits in particular from PEBA’s chemical resistance and it is used for precise geometries for connecting plug-in connections, such as in cannulas.
Which 3D printers can process elastomers like PEBA?
The dominant 3D printers that process PEBA-TPEs as 3D printing material are based on the technology. In the SLS 3D printing process, the powder is sintered layer by layer with a laser, while in the HSS 3D printing process, the powder is selectively colored with an ink and then brought to the melting point with infrared energy. The SLS process is characterized by very high precision and mechanical stability, while the HSS is also very precise and much more productive thanks to print head technology.
You can read about how other materials behave in 3D printing here:
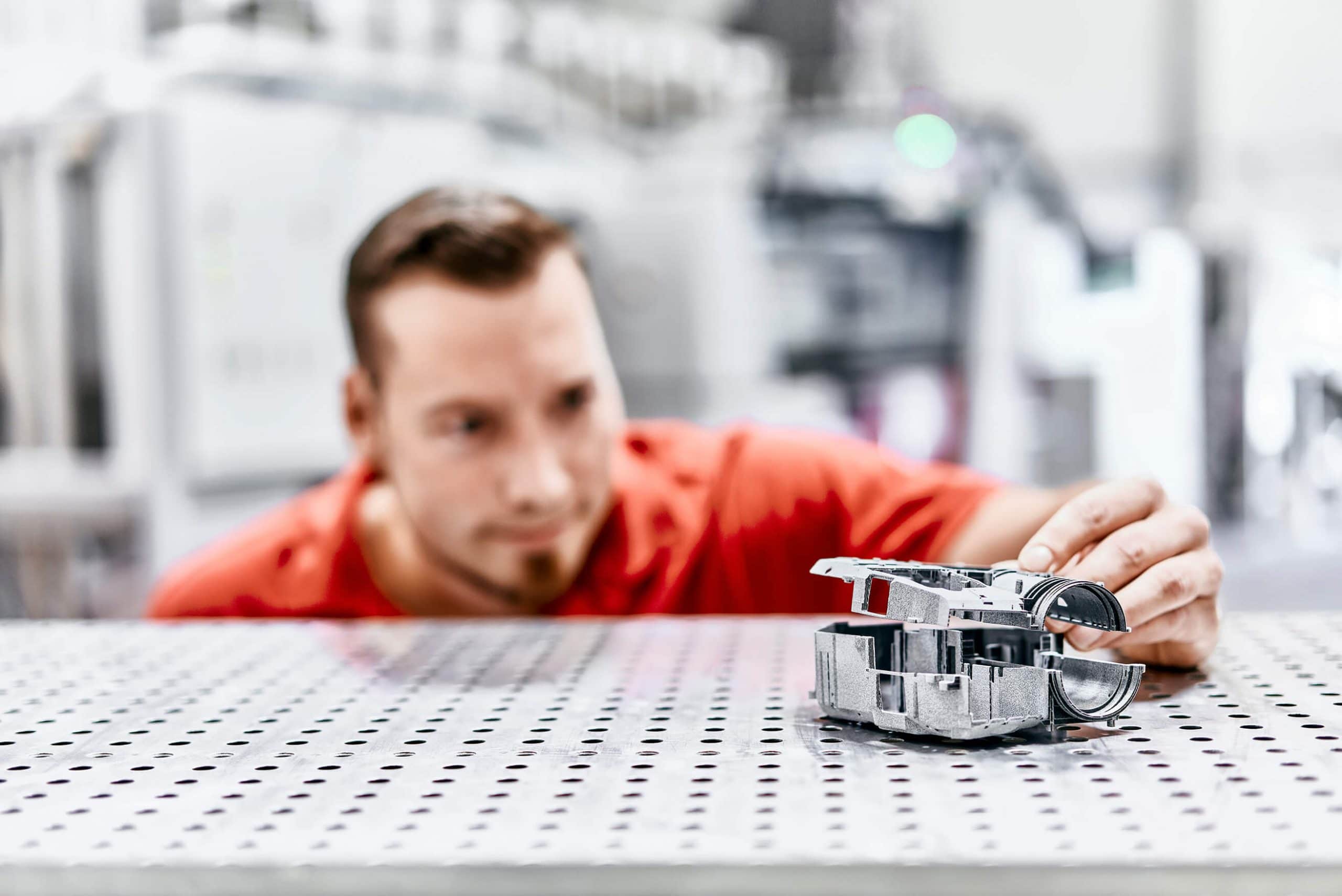
PA12 in 3D printing
PA12 is the all-round talent of polymer 3D printing. As one of the first plastic materials for additive manufacturing, it can be processed with almost any 3D printing technology.
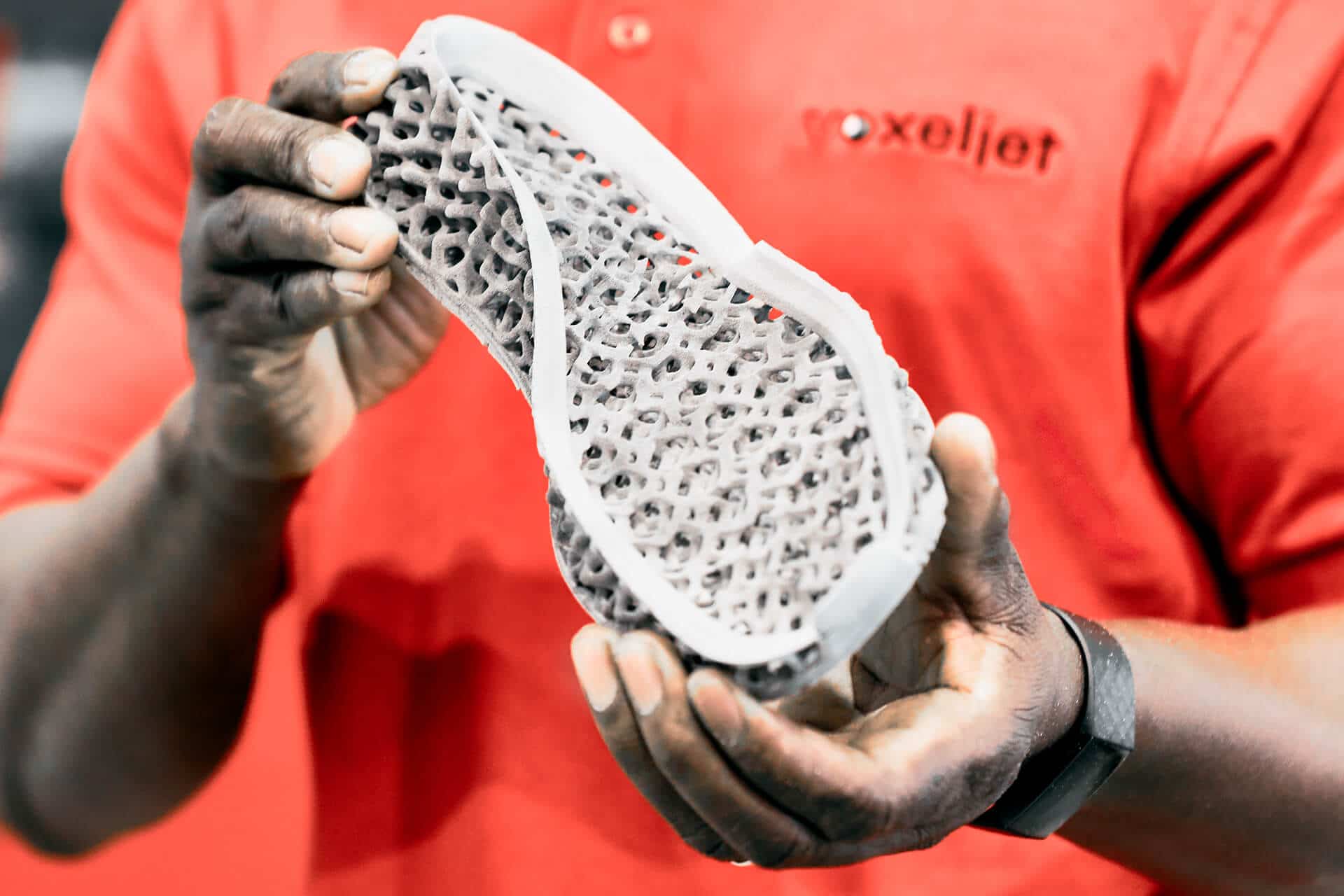
TPU in 3D printing
Solid or flexible. TPU has many applications, especially in the shoe and sports industry. Find out here how the material behaves in additive manufacturing.

PP in 3D printing
PP is one of the most frequently processed plastics in the world. With outstanding material properties, this plastic offers great potential for additive manufacturing.
Additive manufacturing
The world of additive manufacturing is large. Get an overview of the most important processes and applications here.