- Home
- Case Studies
- Aerospace
- Topology optimization in aviation
Creating the aircraft doors of the futureusing 3D printed casting patterns
voxeljet facilitates fast, cost-efficient and flexible precision casting for the French aviation supplier Sogeclair. Sogeclair has found a way to save 30% in weight when constructing aircraft doors.
The French aviation supplier uses 3D-printed PMMA models from voxeljet for tried and tested precision casting. They allow new freedoms in lightweight design and can be produced quickly and cost-efficiently. The aircraft doors of the future were presented for the first time at the Paris aviation show.
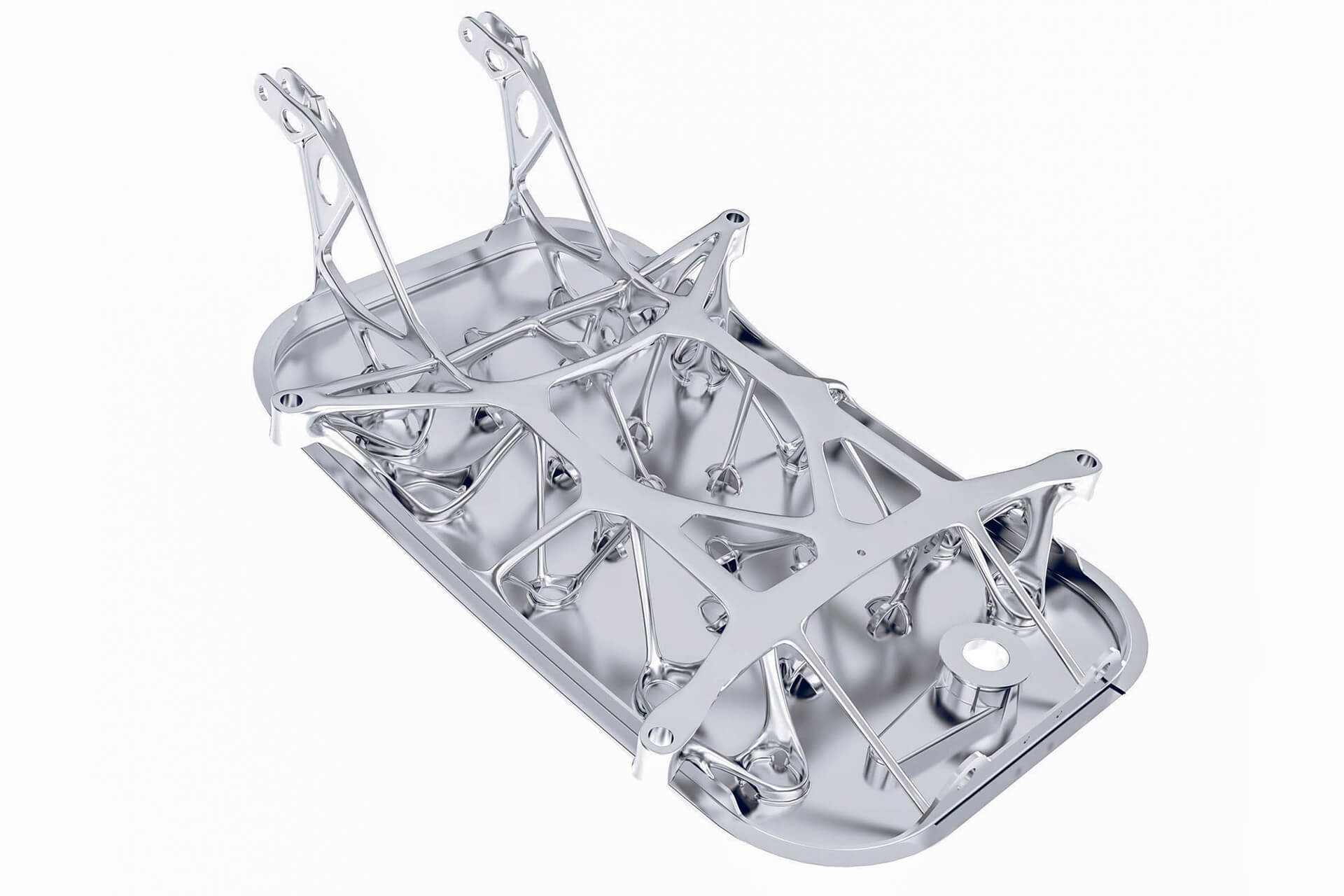
In order to make aircraft more fuel-economical, more and more manufacturers are asking their suppliers for lightweight components. A solution: 3D printing capable of directly producing aluminum and titanium laser sintered components with material-saving geometries. The problem: the finished components are relatively expensive and so far are only suitable for producing small components. Where do we stand with large components such as aircraft doors?
“In this case, 3D printing can be combined with well-tried precision casting,” says Thierry Herrero, West Europe Sales Director for voxeljet. With 3D printing, precision casting models can be printed for geometries not previously manufactured using plastic (PMMA) additives without the need to use expensive special tooling. “This combines the best of both worlds: the geometric freedom of 3D printing and the stability of classic precision casting”.
PMMA models from one of the largest 3D printing systems for casting applications
Sogeclair is included in the users of the 3D-printed moulds. A research project carried out by the French aviation supplier concerns futuristic aircraft doors which, thanks to a refined, bionic network of aluminium struts, present the same strength while using significantly less material and are thus 30% lighter. Creating such a network on a computer with Computer-Aided-Design software (CAD) is no problem for aerospace experts. The difficulty lies in the precision casting process. “For the development of prototypes, companies must make repeated refinements,” explains Herrero. The solution: the VX1000 3D printing system from voxeljet which, with a construction area of 1,000 x 600 x 500 millimetres, is one of the largest industrial 3D printing systems for precision casting models.
It is certainly timely and cost-consuming with each change requiring the production of a new mould for the precision casting. Design changes can be made directly on the screen.
Thierry Herrero, Managing Director voxeljet West Europevoxeljet AG
Even the finest structures can be precisey printed
voxeljet uses the aircraft door CAD file as input for the 3D printing system. This applies an acrylic substance called polymethyl methacrylate (PMMA) in powder form to the construction area in thin 150 micrometre layers. The print head travels over the construction area and bonds the PMMA to the digital blueprint. A fresh powder layer subsequently follows. The precision casting model is built up layer-by-layer, with higher quality than the test prints from the competition.
When the PMMA model has been printed, this is infiltrated with hot wax in order to seal the surfaces. The next step takes place in the foundry. Workers cover the printed model with ceramic layers and smelt the model in a furnace. In the case of ceramic moulds, there are subsequently filled with liquid aluminium. When the metal is cured, workers beat the ceramic layers and expose the finished aircraft door.
“Compared with other additive processable materials, such as liquid resins in stereo lithography, PMMA is excellent for burning out. The main reason for this is the negative expansion coefficient of our powder material, which does not lead to any fractures when burning out the thin-walled model”, says Thierry Herrero, Managing Director voxeljet West Europe, voxeljet AG.
Further Case Studies
Weight reduction through 3D printing: lightweight seats for the aircraft industry
Lightweight seats produced using 3D printing can reduce costs and emissions in the aircraft industry.
3D printed patterns for TITAL, an aluminum and titanium investment casting specialist
Aerospace supplies expert TITAL relies on PMMA 3D printing for investement casting patterns for titanium and aluminium, learn why.
Increase component performance efficiently
How can you increase component performances many times over without adding to the weight?
3D printer manufacturer voxeljet supports Hyperloop project with 3D printed PMMA casting molds for investment casting of aluminium parts
3D Printing Solutions
Would you like to learn more about voxeljet and 3D printing? Click here for the entire voxeljet solution portfolio.