- Home
- Case Studies
- Architecture
- The voxeljet company stone
Detailed concretefacades withindustrial 3D printing:the voxeljet company stone
In the metal casting industry, 3D printing of molds and cores has become almost commonplace. It is a little different in the concrete casting, but that will change. Because the 3D printing of formwork elements has considerable potential, especially for the production of complex, structured and detailed elements. The voxeljet company stone shows what is possible when you combine 3D printing, concrete casting and architectural creativity.
You might think that several stonemasons took months of precision work to carve it out of solid stone – but behind it is a completely different production technique: ultra-modern 3D printing.
Instead of removing material from a solid body, complex shapes are printed and later filled with liquid concrete. The work of art thus combines the latest design techniques with state-of-the-art high-tech concrete and is the basis for unprecedented applications in architecture and construction. In addition to complex curvatures that are difficult to form conventionally, 3D printing is particularly suitable for entire concrete facades or individual facade elements.
3D printing as an additive manufacturing process is conquering new fields of application in a wide variety of industries almost every day. Right at the forefront: voxeljet as a leading manufacturer of industrial 3D printers. Metal foundries have so far been the main users of the processes offered by voxeljet. With the help of 3D printing, highly complex shapes and cores can be produced from sand in the shortest possible time and with a high degree of precision. Users can save entire work steps, such as the construction of expensive molding tools, since only a CAD file is required for the production of 3D-printed sand molds and cores. The voxeljet service center then produces these forms on demand.
Concrete facades for architecture and the construction industry using 3D printing
With the company stone made of concrete, voxeljet is showing new application possibilities for 3D printing in the architecture and construction industry. Just like metal, concrete can also be poured into the sand-printed molds. With the printing of sand molds, both reusable and lost formwork are created, depending on the application and complexity. The advantage of 3D printing lies in the tool-free, cost-optimized manufacturing process. The voxeljet 3D printing systems allow the production of molds with highly complex geometries in the shortest possible time and with impressive precision. With conventional manufacturing methods, such complex shapes would be difficult to manufacture or even completely impossible.
With the casting of the company stone, we were able to produce a geometry that could not have been realised in any conventional way.
Tobias King, Director Marketing and Applicationsvoxeljet AG
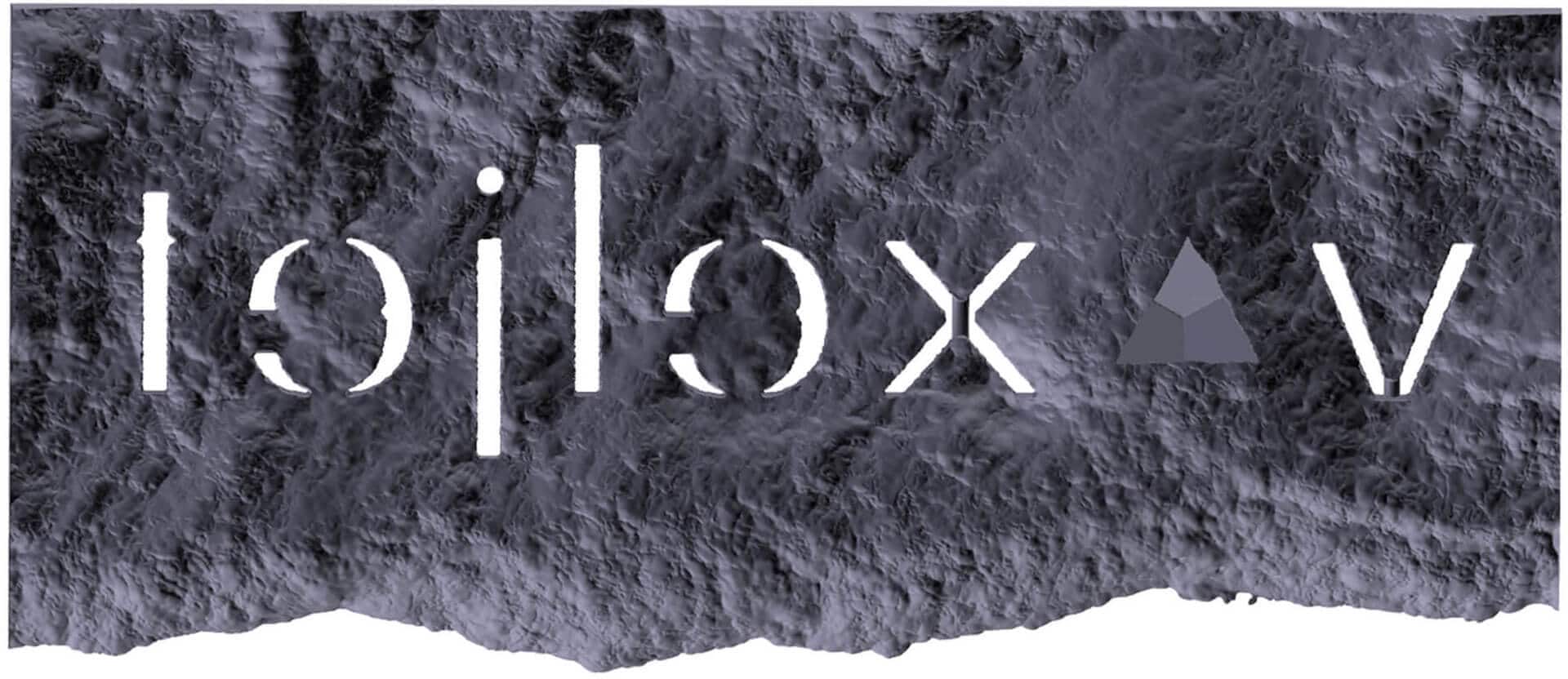
The printing process: from the CAD-file to the finished real life object
At the beginning there is CAD design. In order to fully utilize the advantages of 3D printing, voxeljet opted for a hybrid formwork, a combination of printed and conventional mold elements. The 3D-printed elements were limited to the complex part, the front of the company stone. Simple geometries, such as straight surfaces, are modelled with conventional wooden formwork.
The complex part of the voxeljet company stone consists mainly of the stone structure with the integrated logo, which emerges from the background structure. The design freedom of 3D printing means, that even highly complex geometries with undercuts and intentional unevenness can be realized without any problems.
In order to start the printing process, the finished CAD file was loaded onto a 3D printing system from voxeljet. The 3D printing system then produced the formwork in one go. voxeljet printed the formwork for the company stone on a VX4000, the largest industrial 3D printing system with a continuous building platform of 4x2x1m (LxWxH), in only one night.
The VX4000 applies sand in an extremely thin layer of only 300 micrometers to the building surface. The print head then bonds the layers selectively with a binding agent. Once the mold is fully printed, voxeljet specialists remove the unprinted sand and clean the mold with compressed air. In order to prepare the mold for concrete casting, the 3D printing specialists infiltrated the mold with a PU dispersion to close pores and simultaneously seal the surface.
Perfectly shaped and rich in detail: The casting of the company stone
voxeljet then sent the post-treated form to Dade-Design in Switzerland, so that the concrete casting professionals cast it there. To make it easier to remove the sand mold from the concrete after casting, Dade-Design applies a release agent to the mold.
When it comes to the letters in particular, it is important that the mold can be removed from the casting as easily as possible so that no damage is caused to the concrete later on. is an innovation that opens up completely new dimensions in concrete mold making. 3D printing allows us to use a fully digital production process, saving us valuable time and effort.
Andy Keel, OwnerDade Design
After the printed logo had hardened, Dade Design poured the rest of the company stone in the second step. For this, the concrete foundry used a self-compacting concrete, UHPC (Ultra-High Performance Concrete). The concrete was completely cured after around 20 hours and the formwork could be carefully removed. After removing the formwork, the voxeljet company stone was as good as finished. For the final touch, employees from Dade-Design gave the stone a so-called concrete cosmetic, in which they polished the concrete in order to obtain an even and smooth surface.
The result of the first attempts in concrete casting is impressive. Using state-of-the-art binder jetting 3D printing technology and high level of craftsmanship, 3D printer manufacturer voxeljet has expanded the horizons of traditional casting. “What would have been unthinkable in architecture until a few years ago is now possible through a combination of 3D printing and our specially developed UHPC concrete,” adds concrete casting specialist Keel. With appropriate post-treatment and depending on the application, the 3D-printed formwork elements can also be used several times, for example to enable the production of complex precast concrete parts. The finished stone with the voxeljet logo now decorates the entrance of the voxeljet administration building in Friedberg.
Further Case Studies
For the unique facade of the Galleria Gwanggyo in South Korea, 3D printing and investment casting was employed to create hundreds of individual joint knots for the glass walk.
3D printing and formwork construction in perfection. For a museum in the Black Forest, voxeljet sets new standards for additive manufacturing in architecture.
For an office building near Munich, Deutsche Doka once again used 3D printed formwork elements from voxeljet for concrete casting.
SL Rasch GmbH counts on 3D printing for the visualization of architectural projects.
The Mersitem Wall is a best practice example of how functional and sustainable architecture can be created with 3D printing.
Singapore's AIRLAB uses these table legs to show how architecture can be made more sustainable and functional at the same time.
voxeljet AG prints complex molds for "intelligent" concrete ceiling at DFAB (NEST)
Industrial 3D Printing Systems
Our portfolio of industrial 3D printers ranges from compact systems for research to additive mass production.