- Home
- Case Studies
- Art and Design
- 3D printing the future of prop manufacturing
3D Printing - The future in the film industry
Using 3D printing to create cost-effective and realistic movie props. With Ultra High Definition cinematography hitting our screens, the demand for quality props and models is as high as ever.
While traditional manufacturing methods are still being used, digital technologies such as 3D scanning, 3D modeling and 3D printing have allowed current methods to achieve complexities faster than ever before.
What film and prop makers need to know about 3D printing
From day one, the movie industry has tried to create motion pictures in which everything looks as realistic as possible. Filmmakers and directors have been using a combination of diverse camera tricks, special effects, but also props to make the audience believe what they see is real.
In recent years, 3D printing and scanning technology, also known as additive manufacturing, has brought a revolution to how things are done behind the scenes in the film industry. 3D scanning and printing has been included in the production of a variety of films including Skyfall, Star Wars: The Force Awakens, Guardians of the Galaxy, and Thor: The Dark World. Props in these movies have been used in many different ways and there are several reasons why producers are, increasingly, having props 3D printed.
Some advantages of using 3D printing in the prop and movie industry include the high quality and resolution, scalability, speedy turn around times as well as enhanced customization or design changes that can be achieved without a lot of effort. Glenn Hetrick, a professional in the industry and CEO of Alchemy Studios, voices that 3D printing has helped him to create props that look far more realistic than using traditional methods.
The new way of prop-making
Digital technology sets a new standard for time, flexibility and cost. Prop-makers who see the advantage of those technologies have found them to be very useful:
Details that would take you forever to do, we can now do literally in minutes on the computer, with greater precision and resolution than we can do by hand.Adding 3D printing, we went from taking days to produce a single object to being able to do the same in hours, without waste, and with the added capability of making many more of that same object, to exactly the same high grade specifications.
Neville Page, Concept Designer
Art directors, costume designers, SFX departments and Makeup artists have developed some revolutionary uses of 3D printing. A major advantage in the development stage allows changes in the design to be made instantly, and reproduce them within hours. Discussing ideas in a physical form is a great way to present props and models which engages everyone involved.
Digital files can also save space and solve logistical issues. Storage and welfare of props, crates and fiberglass molds are no longer an issue. Digital files can be sent anywhere in the world within seconds cutting out expensive logistical costs and allowing production to start immediately. Digital files can also save space and solve logistical issues. Storage and welfare of props, crates and fiberglass molds are no longer an issue. Digital files can be sent anywhere in the world within seconds cutting out expensive logistical costs and allowing production to start immediately. Another advantage of a digital file allows items to be printed as large or small as required, and any number of times.
It is therefore not surprisingly that several major productions have made use of these technologies, producing props such as helmets, weapons and a number of ‘back-ground’ scenery drops. Since some original props of previous movies were too valuable and therefore no longer usable, the digital approach was used instead.
A revolution in the prop and movie industry
A recent example is the production of an iconic prop used for a British comedy franchise, Red Dwarf. Phil O’Connell says that “the Red Dwarf crew had ‘Starbug’ 3D printed in order to preserve the original ship from taking any damage on set. The original ship was scanned, 3D printed, epoxied and painted within a week which gave the model crew a time advantage of six weeks compared to traditional reproduction. Added to that, production costs were reduced considerably.
Webinar: Prop making
In this webinar we will walk you through advantages, workflows, materials and plenty of applications & examples of 3D printing-supported prop making.
Further potential for film and other industries
Phil O’Connell has been observing the trend of applying additive manufacturing in the entertainment industry for some time. He argues that “application cases from the world of art, museums and archeology, merchandising to commercials and store design are becoming more common at our 3D service center. The reason is obvious, there is no simpler method for duplicating rare findings and for reconstructing or generating historic templates, statues or skeletons than in 3D printing. 3D scanning is a non-invasive method of digitally replicating objects, and our 3D printers are powerful and big enough to face exciting projects at almost any size. We’ve printed many maquettes for set and light planning, as well as set detailing – let’s see how long it takes to print an entire film set”. Furthermore, “our 3D prints can also be cast in a number of materials using, for example, a two-part silicon mold with a fiberglass jacket”, which is often times used to recreate part of bodies.
As illustrated above, there are several motivations why the production of props through additive manufacturing can be a time saving and economic opportunity. In terms of speed, scalability and complexity, precision and reproduction, as well as fine detailing, 3D printing offers benefits compared to conventional production methods. It is always fascinating to see how the movie industry develops over time to create mesmerizing imagery. For that reason, one should bear in mind that this would not be possible without the work of skilled and talented model makers, sculptors, and 3D printers. Although the production of props may remain the same, the tools used to create them will change.
The process "High Speed Binder Jetting"
Starting off, a 3D model is created on the computer or 3D scanned from a physical object. Creating a digital file allows the props to be optimized to the design production require before finalizing the data for 3D printing. By starting the printing process, a 0.15 mm thin layer of PMMA powder is spread out onto a build platform which is then selectively bonded by a bonding agent, applied via the print head. By repeating these steps, the three-dimensional object is build up layer by layer. After printing, the unbound powder is removed to uncover the raw prop. In order to ready a print for the big screen, prop makers use their skills and bring the prop to life.
A lot of tricks we relied on for decades to bring creatures to life no longer work because you can see the edges, you can see that it was made out of foam and not skin […], 3D design and printing is making the process so much more fluid.
Glenn Hetrick, CEOAlchemy Studios
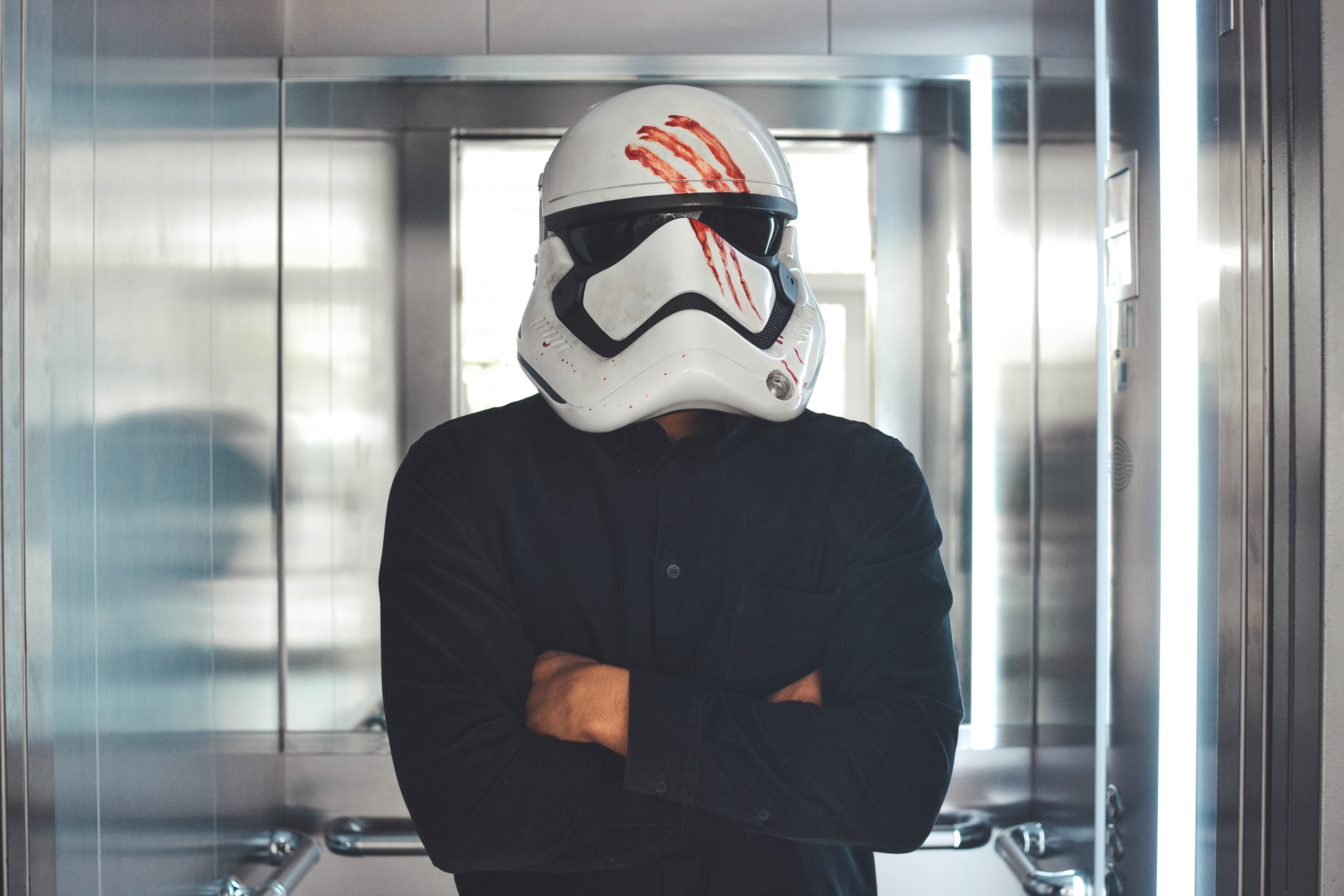
Star Wars Collectables
While 3D printing is relatively new to the Film and Television industry, these technologies have been tried and tested in a variety of ways and already prove successful. That said, we are just at the beginning of the future of model making. With 3D printing, the possibilities are endless.
For further information on how movie props are 3D printed, see the links below:
Further Case Studies
VX4000 expands foundry and business capabilities in water works
By installing a VX4000 3D printer into their new foundry, waterworks specialist Tyler Union not only reduces tooling costs drastically but also positions itself as a forward thinking industry leader.
3D printing for sand casting in Portugal
CINFU is a Portugal-based training and innovation centre for the foundry industry. With a VX1000 3D printer in house, CINFU is gaining significant adaptive advantages for the foundry industry.
Weight reduction through 3D printing: lightweight seats for the aircraft industry
Lightweight seats produced using 3D printing can reduce costs and emissions in the aircraft industry.
Bronze-cast sculptures produced with 3D printing
In the Freedom Monument Sculpture Park, there are three bronze sculptures by artist Shaleigha D'Clark, created using 3D printing
Lanulfi Models optimizes mold making with VX2000
The integration of voxeljet’s VX2000 has redefined Lanulfis approach to metal casting. It offers significant reductions in lead times and enhances design capabilities.
3D-printed sculptures at 2500 metres
At 2,500 metres in the Tyrolean Alps, these 3D-printed sculptures enjoy a special view. They are the fulfilment of a long-held dream of Tyrolean artist Magnus Pöhacker.
3d printed joysticks for tractors and machines
For Lindner Traktorenwerke, 3D printing is already an alternative to injection molding. For example, for customized joysticks and control elements for their tractors.
3D Printing Solutions
Would you like to learn more about voxeljet and 3D printing? Click here for the entire voxeljet solution portfolio.