- Home
- Case Studies
- Automotive
- 3D printing and its applications for racing
3D printing and its applications for racing
3D sand molds used for laminate templates
The Elefant Racing team of the University of Bayreuth proves that sand molds from a 3D printer are not just used as metal casts but are also ideally suited for laminate templates. Students at the university are building the new seat for their race car on the basis of a sand mold printed by voxeljet. The idea of using printed sand molds as positive molds for laminating is as simple as it is ingenious.
The positive mold gives us the option of 'test-sitting' the new seat before laminating, and to make adjustments if necessary. A sand mold is ideally suited for this purpose, since it can be easily machined with sanding and scraping. However, the current mold from the voxeljet printer was a perfect fit from the start.
Artur Horn, Team Manager of Elefant Racing
The seat was printed at the voxeljet service centre exactly according to the design template in the form of several individual components, which were subsequently assembled. Particularly in cases where sand molds will be used multiple times, voxeljet recommends that they are filled and sanded prior to laminating, and that a separation layer is applied. During the laminating process, carbon fibre mats are placed over the printed mold and coated with epoxy resin. This process is repeated until the desired material thickness has been achieved. Finally, the seat was put in a vacuum-packed plastic bag and was cured at room temperature.
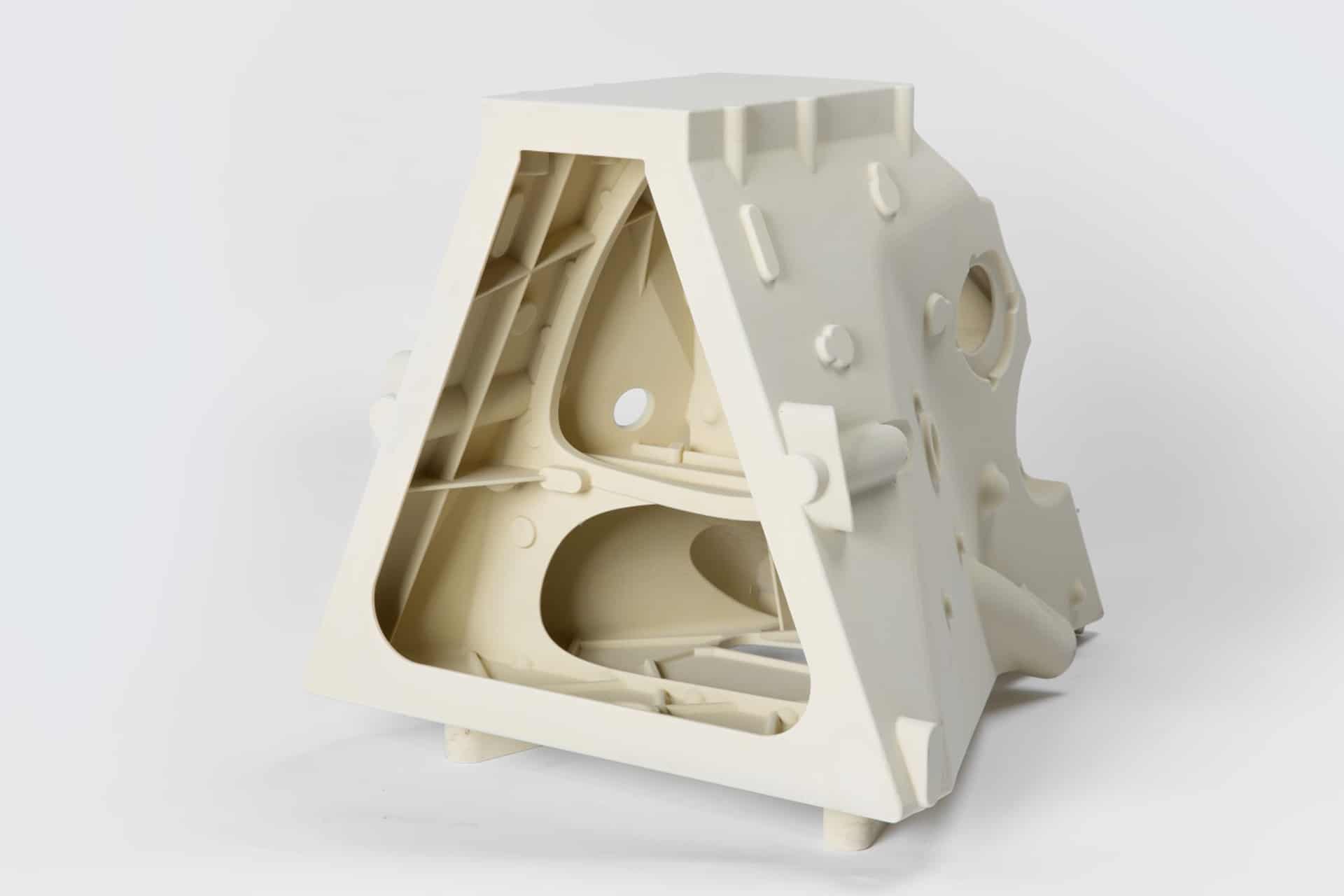
3D printed gearbox housing for Formula 1
R&D doesn`t stop! „If you stop trying to be better, you stop being any good at all” is a quote we are facing at voxeljet every day. With our commitment we are supporting you for decades, seeking for perfection. The gear unit can only be represented in investment casting with the help of additive manufacturing, as manufacturing with tools is too expensive.
3D printed sand mold with furan resin binder for a magnesium wheel carrier
High-tech company voxeljet considers the promotion of innovative approaches and developments at the university level as an important societal responsibility. For this reason, the Augsburg-based company supports the Racetech racing team of Bergakademie Freiberg Technical University – with great success. voxeljet supplied the Racetech racing team with printed sand molds for magnesium sand casting as early as the 2009/2010 racing season. The resulting lightweight-construction components contributed to the Freiberg team’s 14th place out of 475 teams in the world rankings at the end of the season. At this time, the students are working on the new “RT06” race car. Similar to current developments in the automotive industry, which focus on lightweight construction and energy efficiency, work on the RT06 also emphasises weight reduction, including new developments for even lighter wheel mounts and a weight-optimised steering gear housing made of magnesium materials.
Both chassis components are relevant to stability, since high directional and camber stability form the basis for maintaining good control over the race car. The only restriction that had to be taken into account with regard to the new design was a minimum wall thickness of three millimetres, which was specified by the foundry for larger-scale magnesium components.
Once the CAD models for the required molds and cores for the new vehicle components were available, work on the production of the molds commenced at the voxeljet service centre. The modern industrial 3D printers produced the molds made of furan resin-bound molding material within a few days. The molding material is ideally suited for magnesium melting thanks to its low binder content and hence minimal gas formation. A total of four mold sets for the steering gear housing and eight wheel mount mold sets were printed exactly in accordance with the CAD data set, and at accurate voxeljet quality.
Compared to the previous vehicle, the new wheel mounts are approximately ten percent lighter, while the steering gear housing is even 50 percent lighter and the stability of both components has been increased by 20 percent. All in all, it makes for a light and competitive start to the new season for the new RT06 race car.
More Case Studies
3D printing for optimized electric motors
Aiona Cast has filed a patent application to significantly optimize electric motors. The company produced a prototype using 3D printing.
Printed Castings – Optimized housing lets E-Motorcycle Batteries live longer
By using innovative technologies such as 3D printing, the prototype could soon go into series production.
Electric motor housing from the 3D printer
voxeljet 3D printing technology for producing cast parts for electric-mobility
Reverse engineering of a racing engine block
The Binder Jetting technology keeps a classic car on the road
Engine optimization with 3D printing
Vehicle technology manufacturer Lütgemeier increases flexibility and productivity using the voxeljet VX1000 3D printing system in order to supply the high-performance car tuning company Brabus
3D Printing in Reverse Engineering
In the oldtimer sector, more and more spare parts are being manufactured without tools using modern measuring technology in combination with 3D printing.
3D Printing and Motor Manufacturing
Additive manufacturing shortens product time in engine construction and offers faster innovation cycles for individual motor components.
Industrielle 3D-Drucksysteme
Our portfolio of industrial 3D printers ranges from compact systems for research to additive mass production.