- Home
- Case Studies
- Consumer Goods
- 3d printed joysticks for tractors and machines
Eye on the futureInnovation in hand
When it comes to cultivating mountain and grassland landscapes, the family-owned company Lindner tractor company is one of the leading technology powerhouses for agricultural machinery. The Austrian family-owned company has successfully occupied this niche through continuous innovation and development.
In order to meet both the varying structural conditions of mountain landscapes and the individual needs of farmers, Lindner has specialized in state-of-the-art technologies and digitalization in production. One of these pioneering processes is our high-speed sintering 3D printing technology, which Lindner Lindner uses to produce customized joysticks and control levers, gradually replacing injection molding with additive manufacturing.
Injection molding - expensive, generic and inefficient
The manufacturer of agricultural machinery usually employs the conventional injection molding method to manufacture control levers and joysticks. This process entails injecting liquid plastic under pressure into a hollow mold to create two halves of the component, which are then assembled and installed.
However, due to Lindner’s diverse product range and the customized needs of its customers, the company is gradually shifting away from injection molding. Each new design necessitates a new tool, which can be costly and time-consuming.
Additive manufacturing, specifically the HSS technology, offers an efficient and economical solution to this problem. The printing process bonds the polymer material with an ink and infrared energy. This way functional plastic parts can be produced tool-less and with a high degree of precision. Lindner uses this technology to produce different design variants, highly individualized products or new prototypes quickly and without high tooling investments.
“We had to look for alternatives to injection molding production, due to individual inquiries from our customers and the requirements for special small series. WESTCAM, a long standing partner from voxeljet, provided us with competent support in this process and took over the production of the joysticks,” says Manuel Lindner, Head of Innovation & Quality at Lindner.
"We had to look for alternatives to injection molding production, due to individual inquiries from our customers and the requirements for special small series. WESTCAM, a long standing partner from voxeljet, provided us with competent support in this process and took over the production of the joysticks,"
Manuel LindnerHead of Innovation & Quality bei Lindner
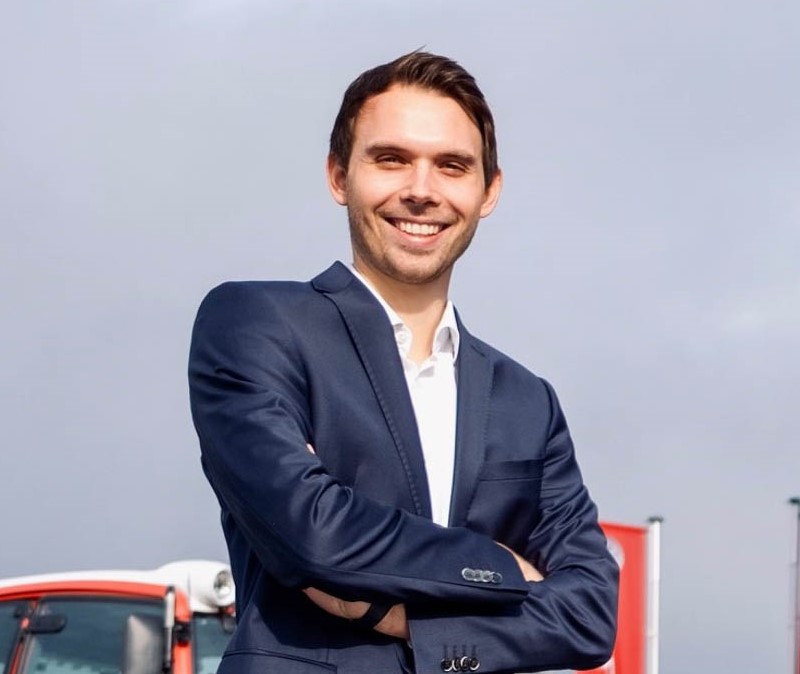
HSS 3D printing enables cost effective series production
Lindner’s joysticks are ideal for additive manufacturing due to their size, complexity, and batch size of around 300 units per year. 3D printing offers an economical solution for the agricultural machinery manufacturer and enables continuous further development of the previously injection molded parts without having to invest heavily in tooling. Printing the joysticks in one piece also reduces assembly effort and allows for easy implementation of individual customer requirements.
However, high-speed sintering technology has an additional advantage over other additive manufacturing technologies, such as selective laser sintering or multi-jet fusion: scalability. The VX1000 HSS, which utilizes industrial print head technology and our expertise in large-format 3D printing systems, is one of the largest and most productive 3D printers for polymers available. The 3D printer for polymers has an build envelope of 1,000 x 540 x 180 mm³, making it one of the largest and most productive 3D printers on the market. This brings the additive series production of polymer components within reach and also offers an economical alternative to conventional injection molding for large series.
The Lindner tractor company uses additive manufacturing to increase flexibility in responding to market demands, accelerate new product development, and meet individual customer needs in a cost-effective manner. This approach provides the family-owned company with economic and competitive advantages, further strengthening its leading position.
More Case Studies
URWAHN – 3D printing in bike manufacturing
To produce its e-bikes, URWAHN has focused on reshoring and lean management and is achieving these goals through additive manufacturing. Learn what role the voxeljet technology plays.
HSS Material Network – Proof of Concept TPU Launhardt
The HSS Material Network has published a new proof of concept. The TPU from the manufacturer Launhardt is one of the softest on the market.
Industrial Polymer 3D Printing Review: An extensive comparison of voxeljet HSS, HP MJF, and SLS
Whats the difference between HSS, MJF and SLS polymer 3D printing? Get to know the three main AM technologies for polymers in this extensive comparison.
HSS Material Network – Proof of Concept HDPE
Together with Fraunhofer IPA we have qualified the polymer HDPE for additive manufacturing within our HSS Material Network.
HP Multi Jet Fusion and voxeljet High Speed Sintering in comparison
The 3D printing processes MJF and HSS in comparison: Where are the differences and advantages for users?
Polymer sintering in custom mechanical engineering
With High Speed Polymer Sintering, prototypes can be realized much faster and economically viable.
3D printing for the perfect sneaker
How polymer high speed sintering (HSS) can be used to develop the perfect 3D printed shoe.
Industrial 3D printers
Our portfolio of industrial 3D printers ranges from compact systems for research to additive series production.