- Home
- Case Studies
- Consumer Goods
- 3D printing for the perfect sneaker
3D printed sneaker -The Coral Runner shoe
Sneakers have become an established part of our everyday life. At the same time however, the shoe industry is also confronted with a number of challenges. The Coral Runner, a unique shoe design by Singapore shoe designer Shun Pin Pek, shows how additive manufacturing can meet these challenges.
Feet are probably one of the most underestimated body parts we have. Next to our hands they are one of the main elements of our locomotor system and carry us – in the best case and in the truest sense of the word – to the end of our lives.
So, it is not surprising that mankind started to protect their feet at an early age. Thus, the (at that time still very rudimentary) shoe was invented. The oldest archaeological findings date shoes back to the year 3500 BC. Over time, the shoe itself has enjoyed increasing attention and popularity. Particularly, in recent decades. Above all, the sneaker. From 2012-2019 alone, the worldwide turnover of sneakers has increased from 30.4 billion euros to 61.7 billion euros. By 2025, sales are forecast to increase to up to 91.0 billion euros. It is therefore no wonder that sporting goods manufacturers invest millions in the further development of their sneaker portfolio.
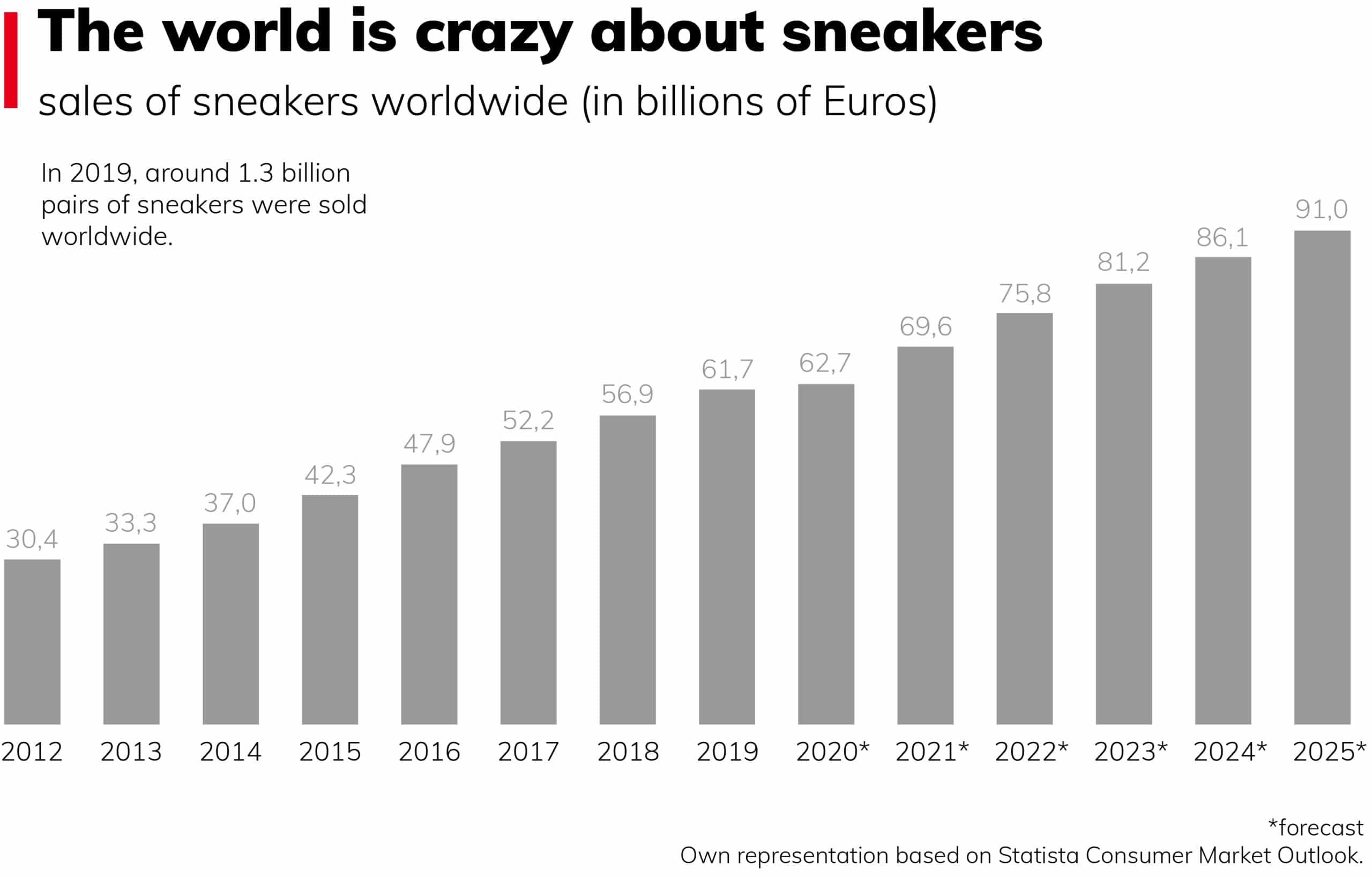
At the same time, however, the shoe industry faces a number of challenges:
- Individualization: customers are placing more and more value on customized shoes that are perfectly adapted to their feet and movements for improved comfort and performance.
- Sustainability: plastic in particular is currently experiencing a kind of image crisis. Plus: too much different materials make it hard to recycle reasonably.
- Automation: Individualization means small quantities. Small quantities in turn require special tooling or molds, which again result in high costs for companies and long delivery times for customers.
This is where 3D printing comes into play, as it can address all these challenges effectively
CAD data – the latest scanning technologies deliver high-quality CAD data that represent an exact digital image of the examined foot. Simulations are used to analyze the walking behavior and transferred accordingly to an individualized virtual shoe sole. This data serves as a design template for additive manufacturing.
Geometric freedom – The data and the representative shoe sole can be optimized in terms of material consumption. Material is only used where it is necessary and appropriate. New complex shapes and structures are providing new features that can be incorporated. All possible without the need for tooling, enabling more possibilities on adjusted material characteristics.
Industry 4.0 – Over the past decades, 3D printing has continuously evolved into a highly productive and automatable production technology. This opens the way for automated mass production of customized products.
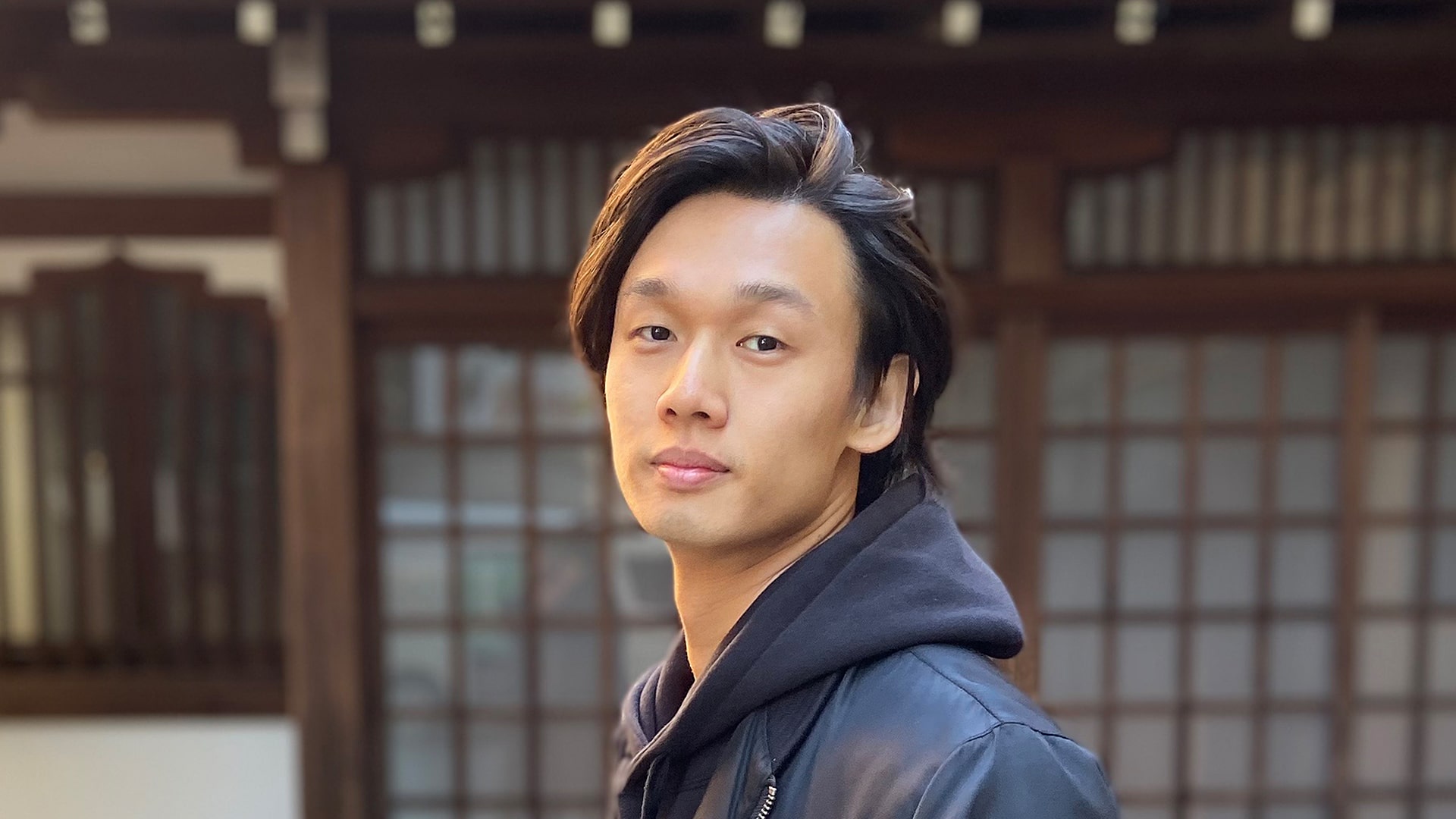
These challenges and trends are no novelty for product and shoe designers like Shun Ping Pek for example, a shoe designer from Tokyo. Since his childhood he has been enthusiastic about the creation of products and studied product design at the Nanyang Technology University in Singapore. At the Pensole Design Academy in Portland, USA he deepened his passion and know-how for footwear design with an in-depth course for footwear design.
As for many of us, shoes are an integral part of Shun Ping Pek’s daily life. When he bought his first 3D printer in 2017, he began to look more closely at them. Fascinated by the challenges of making shoes as well as the endless possibilities of 3D printing. The shoe designer draws his inspiration for his designs from his environment. No matter if it is objects, patterns or naturalistic elements he encounters in his day-to-day life. This actually gave him the idea for his “Coral Runner” shoe concepts.
As the name suggests, corals, or more precisely the growth of corals, influenced the ideas for this shoe. Which, especially with regard to 3D printing, is quite appropriate. Metaphorically speaking, both corals and 3D printing follow a similar growth strategy. With the Coral Runner, Shun Ping wants to draw a parallel to the idea of the corals growing within the powder bed of a 3D printer, just as they would in their natural habitat.
The geometry is both simple and complex. While the overall design of the shoe is kept as simple as possible, the complex tube structures serve as reinforcements on the surface and simultaneously as a profile on the shoe sole. Thus, the entire shoe consists of only one single element. Without seams, adhesive or fasteners.
To produce an initial prototype of the shoe, Shun Ping Pek decided to work with voxeljet, who with their high speed sintering technology offer a suitable polymer 3D printing process.
HSS – the choice for fast prototyping
The 3D printer VX200 HSS from voxeljet proved to be the right choice for producing the first design iteration of the Coral Runner. On the one hand, because the printing system works very fast with constant layer times, and on the other hand, it is capable of processing a wide range of polymers.
Webinar: HSS 3D printing
In this workshop we will present our HSS technology in detail: From open source conception to scaling and production possibilities.
The great advantage of 3D printing is both on-demand manufacturing and the one-to-one transfer of the digital model into a real object. While the Coral Runner could theoretically also be manufactured using conventional production techniques such as injection molding, this way would have been very challenging due to the consistent design. The HSS technology offers the ideal solution.
Shun Ping Pek, Designer
The shoe was printed in TPU from material manufacturer Covestro, a material newly qualified especially for the HSS process. A highly resilient, thermoplastic material that has been used in the production of shoe soles for decades. With the HSS technology voxeljet can process various polymers. These include the classic PA12, but also polypropylene, EVA, PEBA or, as with the Coral Runner TPU.
The choice of TPU made perfect sense in this case, since it has several exciting properties. It can be very soft and elastic or very hard and durable. With the help of our HSS technology, these properties can be influenced in all three dimensions.
This property definition is made possible through the so-called grayscale printing. By specifically controlling the volume of the absorber jetted into the powder bed, certain construction areas can be dyed more deeply. The more absorber is jetted, the stronger the components become. By using industrial inkjet print heads, it is thus possible to print different gray scales within one layer and thus establish different product properties in just one layer. In regard to shoes, the sole can thus be perfectly adapted to individual tread patterns and cushioning requirements.
In the course of the Coral Runner, the design was repeatedly adapted to the process in order to finalize the design, which is both geometrically and functionally modified to the HSS process.
Learning by doing
Each design iteration could be realized without tools within a few days: The data can be quickly edited on the computer and can be immediately transferred to the printing system to hold the product in your hands as soon as possible, test its properties and re-evaluate the design again if necessary. That’s the great strength of 3D printing. It’s possible to react in the shortest possible time to accelerate product evolution and qualification.
Both for the designer and for voxeljet the project has been a steep learning curve. Evaluating the maximum wall thickness was one of the biggest challenges to ensure sufficient flexibility of the shoe while reducing the weight and material required. However, this was quickly overcome through rapid digital adaptation of the design and subsequent 3D printing.
I learned that HSS technology allows for faster print when compared to traditional Selective Laser Sintering (SLS). Taking into consideration on how the technology works, I am able to create improved functional designs. I believe with the increased efficiency of the technology, e.g. on larger platforms like the VX1000, I see the potential of HSS being adapted beyond prototyping and into mass manufacturing.
Shun Ping Pek, Designer
voxeljet however is already working on scaling the HSS process to a VX1000 HSS. A 3D printing system that demonstrates its strengths particularly in the production of larger quantities up to fully automated series production. And who knows, maybe 3D-printed shoes will soon carry us through the next 3,500 years.
More Case Studies
3d printed joysticks for tractors and machines
For Lindner Traktorenwerke, 3D printing is already an alternative to injection molding. For example, for customized joysticks and control elements for their tractors.
URWAHN – 3D printing in bike manufacturing
To produce its e-bikes, URWAHN has focused on reshoring and lean management and is achieving these goals through additive manufacturing. Learn what role the voxeljet technology plays.
HSS Material Network – Proof of Concept TPU Launhardt
The HSS Material Network has published a new proof of concept. The TPU from the manufacturer Launhardt is one of the softest on the market.
Industrial Polymer 3D Printing Review: An extensive comparison of voxeljet HSS, HP MJF, and SLS
Whats the difference between HSS, MJF and SLS polymer 3D printing? Get to know the three main AM technologies for polymers in this extensive comparison.
HSS Material Network – Proof of Concept HDPE
Together with Fraunhofer IPA we have qualified the polymer HDPE for additive manufacturing within our HSS Material Network.
HP Multi Jet Fusion and voxeljet High Speed Sintering in comparison
The 3D printing processes MJF and HSS in comparison: Where are the differences and advantages for users?
Polymer sintering in custom mechanical engineering
With High Speed Polymer Sintering, prototypes can be realized much faster and economically viable.
Industrial 3D Printing Systems
Our portfolio of industrial 3D printers ranges from compact systems for research to additive mass production.