- Home
- Case Studies
- Foundry
- 3D printed prototype of a cylinder head
Additive manufacturingprocess realized MAN cylinder head
A cylinder head weighing several tonnes was produced at MAN B&W Diesel AG in Augsburg in record time, confirming the usefulness of the newest mold production technologies.
A company presentation by MAN B&W Diesel AG states as follows: “Diesel engines consist of 70% to 80% cast components, therefore our foundry is mainly concerned with the production of these components at the required quality and market-appropriate prices.” MAN B&W Diesel AG Augsburg is measuring its performance by this requirement as part of its daily operations. But is it also possible to produce a large diesel cylinder head in two weeks?
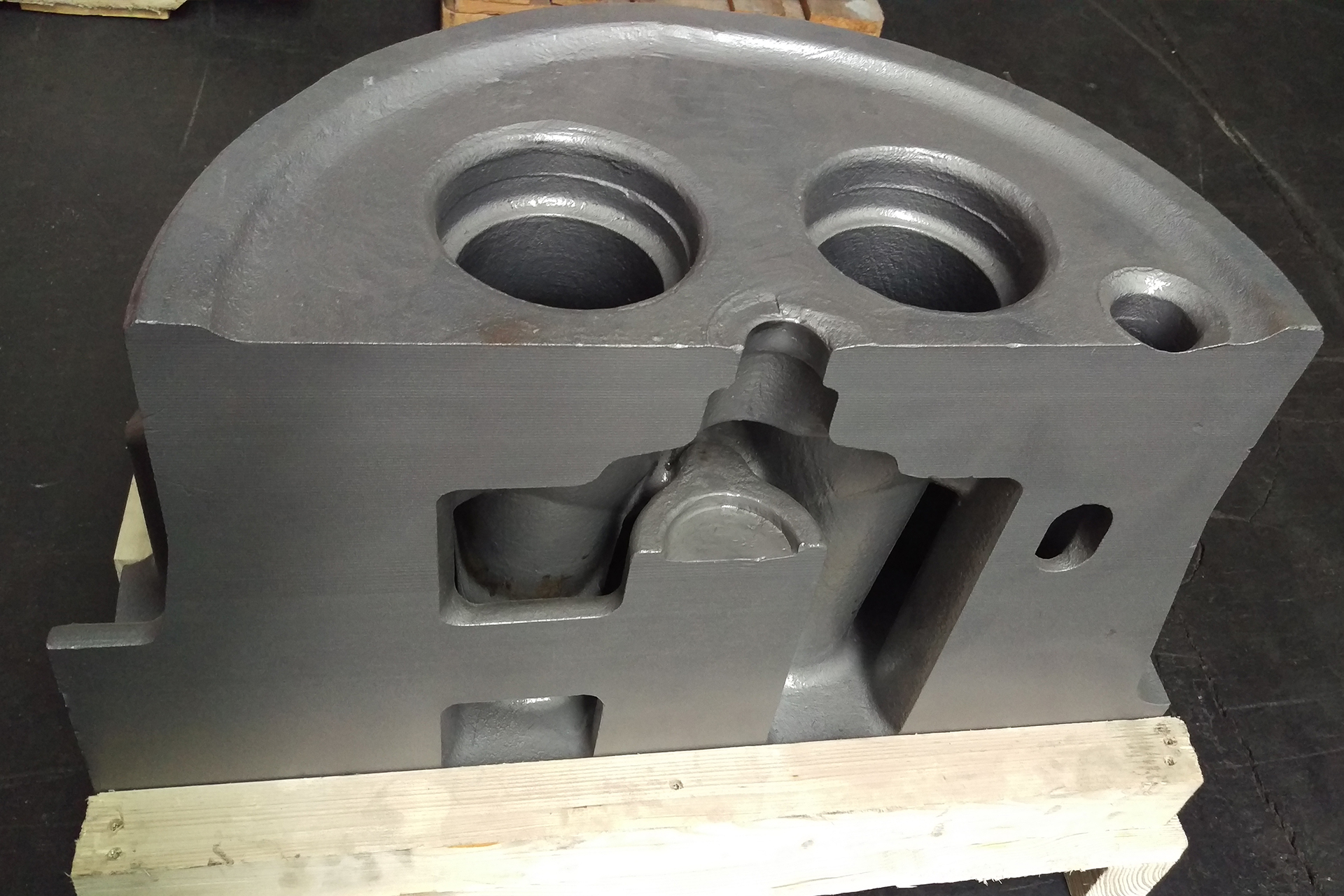
Challenge: Very large model with many undercuts
In contrast to a conventional mold structure, which consists of a top and bottom box as well as 19 cores, seven of which featuring different geometries, the mold was merely divided in half. The two halves of the mold contained the gating system, feeder heads and the downsprue. To ensure that chills could continue to be placed on the combustion space side, the front cover was separated from the mold and implemented in a conventional manner using core boxes.
Solution: Mold parting for cylinder Head
The molding material consisted of sand with an average grain size of 190 µm, which was processed at a layer height of 0.4 mm. The system required about 28 hours to build one half of the mold with the external dimensions 1,460 x 741 x 600 mm. Despite the presence of massive undercuts, it was relatively easy to clean the mold.
A variety of precautions were taken during the 3D sand mold design process to ensure the safe handling and transport of the molded parts: For example, each half featured continuous longitudinal bores for attaching the turnover boards. Similarly, the freely suspended inlet and outlet cores were built with back braces, which could easily be removed at MAN B&W. Not least, the good stability of the molded parts also ensured that no transport damages occurred during the entire project.
The whole process only took four days after the data was transmitted. The material EN-GJS 400-15 was cast at 1360 °C. The first cast could be performed after almost two weeks.
Further Case Studies
CINFU is a Portugal-based training and innovation centre for the foundry industry. With a VX1000 3D printer in house, CINFU is gaining significant adaptive advantages for the foundry industry.
The integration of voxeljet’s VX2000 has redefined Lanulfis approach to metal casting. It offers significant reductions in lead times and enhances design capabilities.
Express Prototyping belongs to the leading experts for 3D printing investement casting patterns in North America. Learn from the CEO Thomas Müller how he established the business and how he sees the future.
Using the combination of sand and 3D printing, the British foundry Boro Foundry was able to produce a flawless spare part for a steam locomotive.
Aiona Cast has filed a patent application to significantly optimize electric motors. The company produced a prototype using 3D printing.
With a new VX2000, a 3D sand printer for metal casting, Hetitec produces finished castings in a matter of days.
Whether it’s aerospace, automotive or design applications, the us-based award-winning foundry Aristo Cast counts on 3D printed patters for investment casting.
Industrial 3D Printing Systems
Our portfolio of industrial 3D printers ranges from compact systems for research to additive mass production.