- Home
- Case Studies
- Foundry
- 3D printing saves costs in sand casting
3D printingsaves up to 75%in sand casting costs
3D printing brings time and cost saving advantages when compared to conventional manufacturing. In direct comparison to conventional production, 3D printing illustrates a clear cost profit. When the production in conventional production lies at around 3,600 € the production with 3D printing can be reduced to 900 €.
3D printing does not only help save costs, as illustrated, but it also helps dramatically shorten the production process for molds and cores. Entire steps, including expensive tool costs, among other things, can be eliminated, since only one CAD data set is needed to produce sand molds and cores.
Producing sand molds and cores without tools makes economical production possible, from individual parts to small batches. Unlike with conventional production methods, there is almost no limit to the complexity of molds and cores in 3D printing. After all, the effort involved in additive manufacturing does not depend on component complexity.
These factors are particularly apparent in the specific case of manufacturing a sand core for a turbine wheel. With conventional methods, the individual core segments of the turbine blades must be laboriously assembled into a core. With 3D printing, however, the entire turbine core is produced as a single piece. This significantly shortens the entire production process, since the step of assembling the core is eliminated. This means that up to 75% of the costs can be cut in smaller batches.
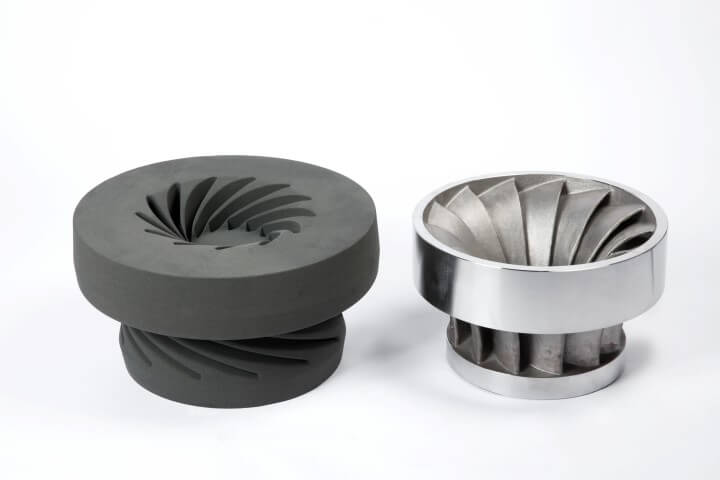
Economical production, from prototypes to small batches
Short delivery times and a high degree of flexibility play a crucial role in meeting a wide range of requirements. But how do we link these two factors reasonably and, most importantly, economically?
It takes only a few days to produce sand molds and cores with the voxeljet 3D printing process Binder Jetting. This saves several weeks of time, compared to conventional production methods. It also increases flexibility in many respects. First of all, there is no need to worry about undercuts or draft angles.
In addition, necessary casting devices such as the deadhead system can be built right into the molding box and printed. Changes to the component can also be made quickly and easily. The goal is to significantly reduce the amount of time and money involved in producing the mold and core and to easily implement complex geometries. 3D printing and conventional manufacturing can also be combined at will.
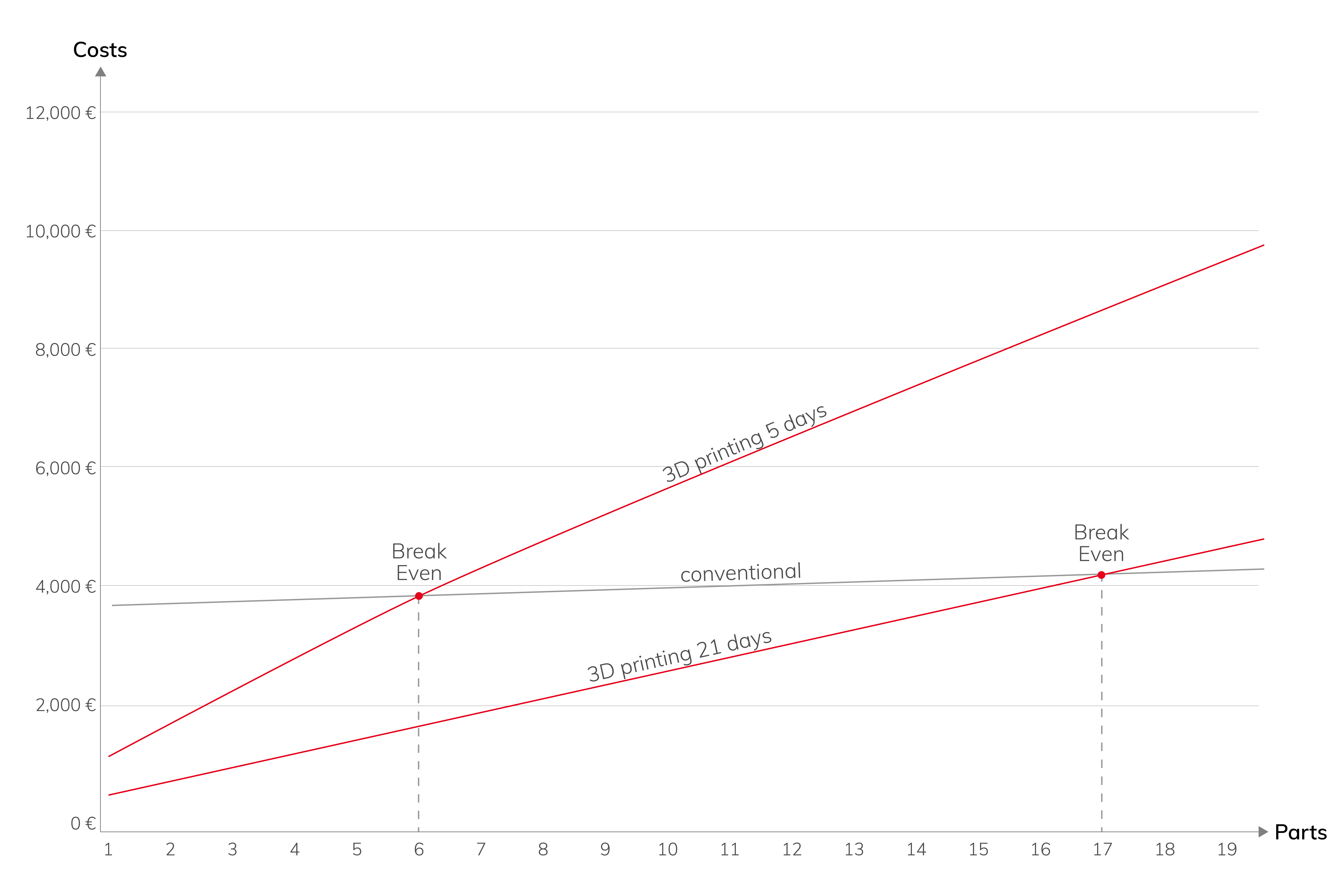
3D Printing Sand molds and cores of any complexity are produced in a layering process. A recoater distributes the particulate material in a very thin layer over the entire build space. A print head then selectively applies binder to the areas where the component will be produced later on. These two steps continue to be repeated until the entire component has been built. The loose particulate material is subsequently removed from the component, which is then post-processed.
From printed core to finished cast part
Blacking Like with classic sand casting, the printed core is also provided with a black wash in the foundry so that it can withstand the high thermal loads.
Mounting the core The 3D-printed sand core is subsequently inserted into a conventionally produced mold. Conventional production methods and 3D printing can generally be combined at will.
Casting The turbine wheel is now cast. All common alloys can be cast with the 3D-printed molds and/or cores. Different sand granulations can be used to influence the surface quality.
Removing the core Like with conventional production methods, 3D printing of sand molds and cores is a lost-mold casting method.
Post-processing The component is post-processed after it is removed from the mold. The amount of post-processing work required is reduced by the 3D printing process, since cast parts are already more accurate. This is due to the fact that even complex geometries with undercuts can be printed as a single piece.
Benefits of 3D printing at a glance
- Time savings and cost savings with short throughput times and tool-free production.
- High flexibility in terms of number of pieces and mold design.
- Hybrid design by means of combination with conventional processes.
- No storage & maintenance costs for conventional sand molds and sand cores.
Further Case Studies
3D printing for sand casting in Portugal
CINFU is a Portugal-based training and innovation centre for the foundry industry. With a VX1000 3D printer in house, CINFU is gaining significant adaptive advantages for the foundry industry.
Lanulfi Models optimizes mold making with VX2000
The integration of voxeljet’s VX2000 has redefined Lanulfis approach to metal casting. It offers significant reductions in lead times and enhances design capabilities.
PMMA 3D printing conquers North America
Express Prototyping belongs to the leading experts for 3D printing investement casting patterns in North America. Learn from the CEO Thomas Müller how he established the business and how he sees the future.
Boro Foundry – Superheater Header
Using the combination of sand and 3D printing, the British foundry Boro Foundry was able to produce a flawless spare part for a steam locomotive.
3D printing for optimized electric motors
Aiona Cast has filed a patent application to significantly optimize electric motors. The company produced a prototype using 3D printing.
With a new VX2000, a 3D sand printer for metal casting, Hetitec produces finished castings in a matter of days.
Printed castings for investment casting
Whether it’s aerospace, automotive or design applications, the us-based award-winning foundry Aristo Cast counts on 3D printed patters for investment casting.
Industrial 3D Printing Systems
Our portfolio of industrial 3D printers ranges from compact systems for research to additive mass production.