Industries
3D printing in the automotive industry
Automotive additive manufacturing. Fit for fast innovation cycles.
- Home
- Additive Manufacturing
- Industries
- Automotive industry
Current applications and future prospects of additive manufacturing in the automotive industry
When it comes to implementing new technologies, the automotive industry always takes a pioneering role. Assembly line work and the use of industrial robots pay off in factors such as precision and efficiency in the assembly of cars. Additive manufacturing for automotive parts contributes to increased flexibility, agility and resource efficiency of modern production lines.
Although automotive 3D printing systems have yet to produce a whole car, many automotive parts are already being manufactured additively today. This is primarily due to increased customer needs, stricter environmental regulations with regard to sustainability, and alternative powertrains and individualization, among others.
This requires a technology with which prototypes can be produced quickly and product development cycles can be shortened. Complex components must be produced economically in batch sizes. 3D printing for automotive applications is the solution.
The advantages of additive manufacturing in automotive industry - 3D printed car parts pave the way for tomorrow's mobility
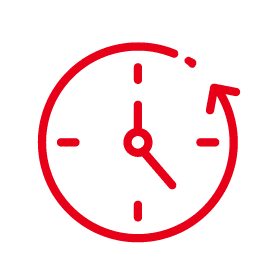
Time
By eliminating the need for tool or mold making, automotive additive manufacturing production processes can shorten manufacturing times of components by up to 75%. This is true for product development in model and prototype construction, as well as in the production of small and medium-sized series or in the manufacture of complex or variant-rich components.
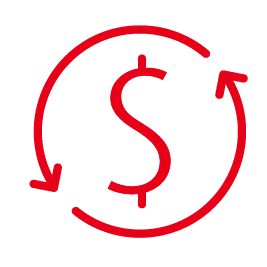
Costs
Complex geometries, structures and surfaces and precisely fitting components: conventional processes are quick to reach their economic limits due to cost-intensive mold making. One of biggest advantages of additive manufacturing in the automotive industry is the economic benefit - both for individual and for series components.
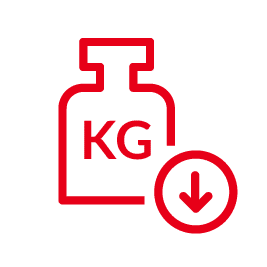
Weight
3D printing in automotive manufacturing enables geometric freedom. Even the most complex lightweight designs and topologically optimized or generatively designed components can be implemented with ease. Vehicles become lighter, fuel consumption is reduced, and design options become more diverse.
Thanks to this printing system as well as the complete post-processing "in-house" up to quality assurance, we were able to achieve time savings of up to 60% in the production of complex and high-quality sand casting molds.
Jochen Hülsmann, Managing DirectorLütgemeier GmbH
voxeljet 3D printing supports innovative vehicle technology
3D printing for the engine and powertrain
The advantages of 3D printing are particularly evident in the additive manufacturing of engine parts in the automobile industry. Thanks to the layer-based production process, engineers are no longer bound by the limits of conventional manufacturing.
“Design for Manufacturing”, i.e. the design of a component for producibility in high volumes, is being replaced by “Design for Functionality”, i.e. optimization for functionality. Here, functional design is both a process and a result – the goal is to perfectly adapt a component to its requirements and tasks. For example, automotive 3D printing can be used to optimize an engine and its multitude of components in such a way that consumption is reduced, performance and efficiency are increased, materials are saved, and the weight of the vehicle is reduced.
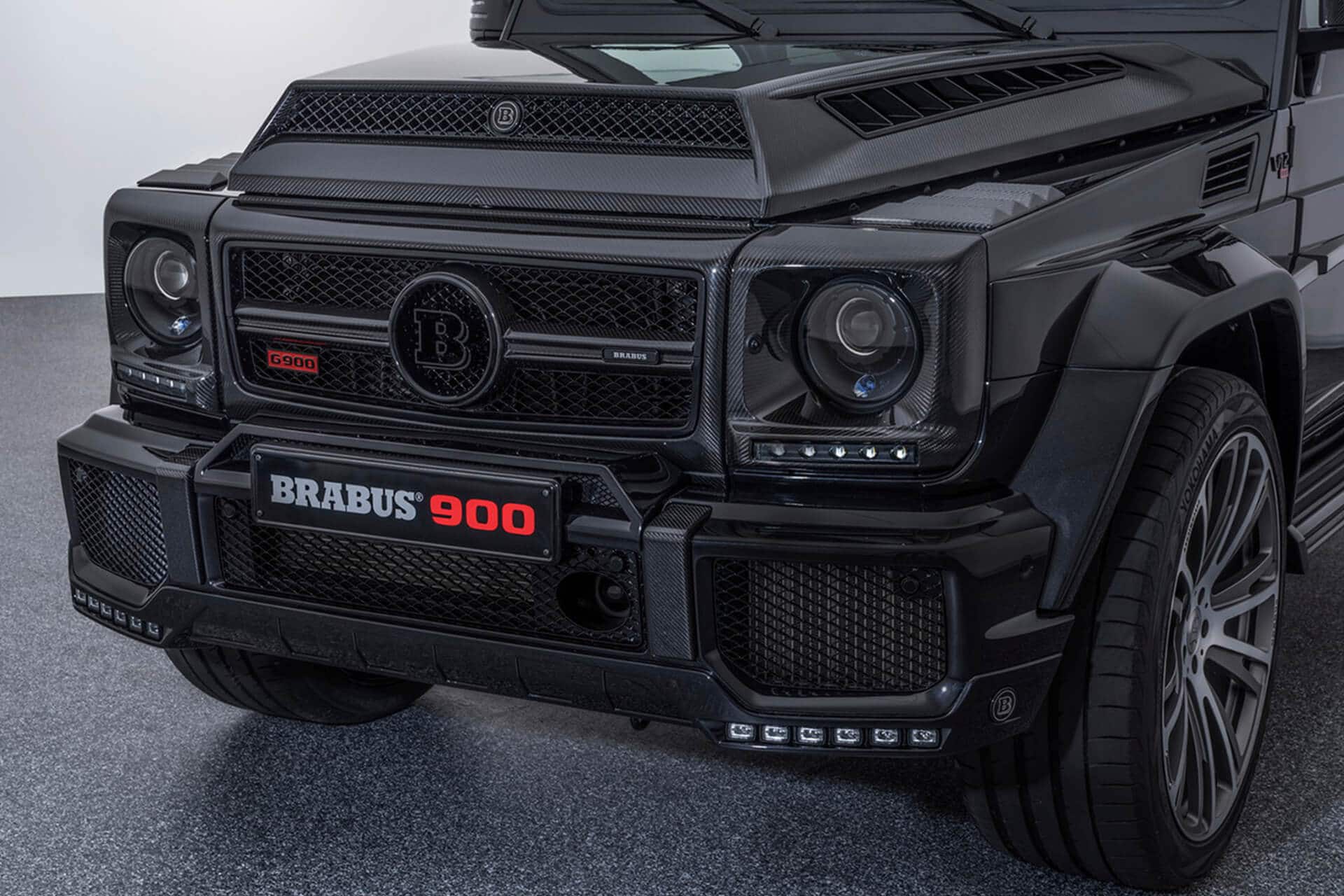
Motor optimization using 3D printing
voxeljet additive manufacturing solutions for applications in the automotive industry enable Lütgemeier GmbH, a vehicle technology manufacturer, to create complex molds for metal casting.
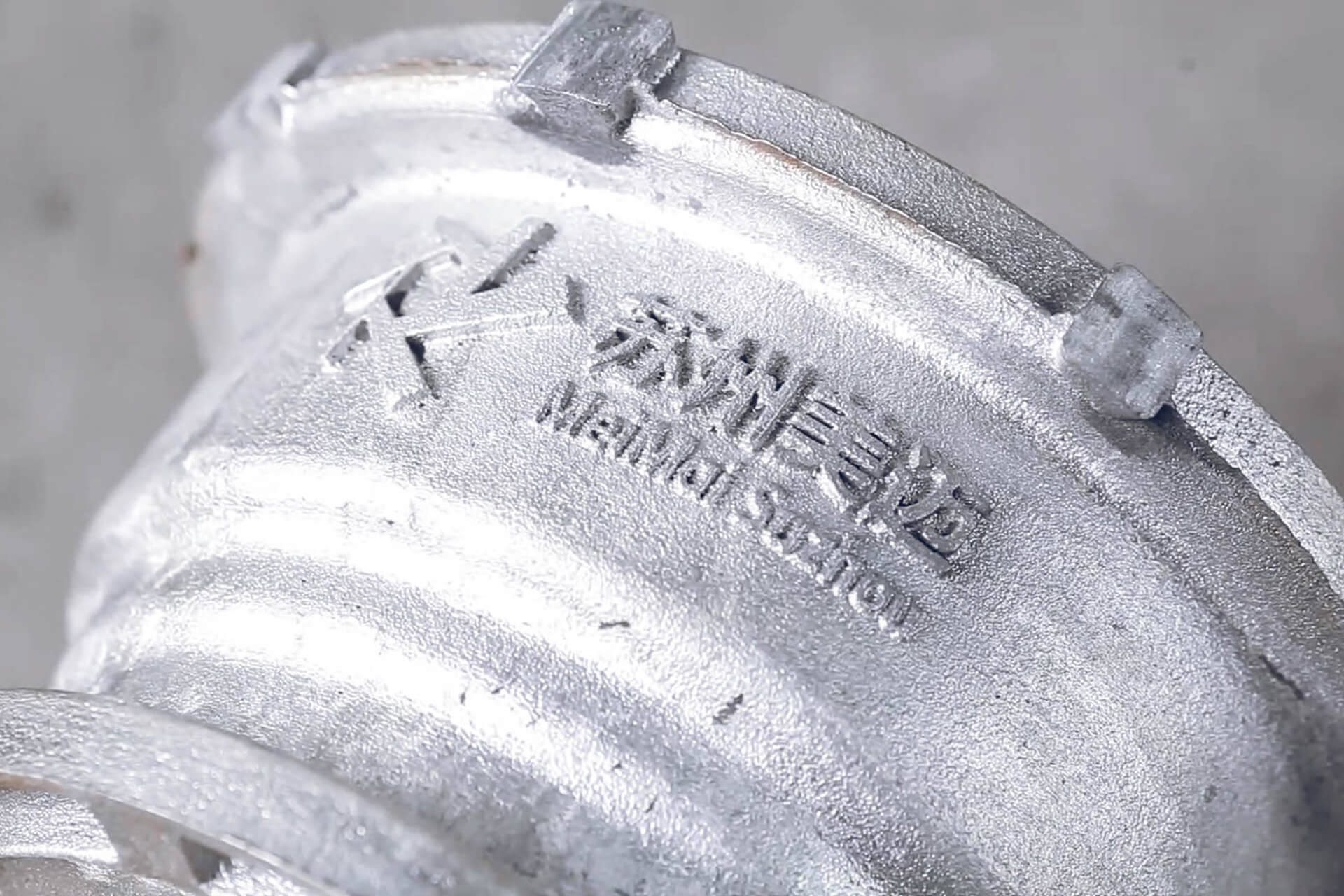
Electric motor housing from 3D printer
Electric motor housing from an industrial 3D printer enables foundries to produce electric car motor components.
3D printing for the vehicle chassis and structural components
While many technologies and users focus on engine components, trim or structural elements usually still receive little attention. But 3D printing also offers potential applications outside the engine compartment. Here, voxeljet’s Universal Binder Jetting technology, which is geared towards large-format applications, opens new doors.
Using large-format 3D sand printing, entire molds and cores for body elements or structural components can be additively manufactured and subsequently cast. Whether underbodies, suspension beams or bumpers, the possibilities for 3D printing automotive parts are as diverse as they are demanding. Here, too, lightweight construction and functional optimization are the decisive factors that will pave the way for a new generation of cars.
3D printing for the car interior
Sand and metal are rarely found in car interiors or are not visible to the naked eye. Instead, plastics are used for the production of trim elements, such as dashboards or control elements. The additive manufacturing of automotive parts can be done using voxeljet’s High-Speed Sintering (HSS) process. Here, 3D printing offers the automotive industry not only economic but also image-oriented advantages in the form of customizable production.
Elements of the operator ergonomics (steering wheels, knobs, switches or buttons) or even the seat ergonomics can be individually adapted to the wishes or needs of the customer, 3D printed and installed. Due to the continuous further development of the technology, additive manufacturing is also moving for such application purposes from a technology primarily used in prototype construction to an economical production process for variant-rich series production.
More case studies in the automotive industry
3D printing for optimized electric motors
Aiona Cast has filed a patent application to significantly optimize electric motors. The company produced a prototype using 3D printing.
Printed Castings – Optimized housing lets E-Motorcycle Batteries live longer
By using innovative technologies such as 3D printing, the prototype could soon go into series production.
Electric motor housing from the 3D printer
voxeljet 3D printing technology for producing cast parts for electric-mobility
Reverse engineering of a racing engine block
The Binder Jetting technology keeps a classic car on the road
Engine optimization with 3D printing
Vehicle technology manufacturer Lütgemeier increases flexibility and productivity using the voxeljet VX1000 3D printing system in order to supply the high-performance car tuning company Brabus
3D Printing in Reverse Engineering
In the oldtimer sector, more and more spare parts are being manufactured without tools using modern measuring technology in combination with 3D printing.
3D printing and its applications for racing
3D printing provides racing with the ability to quickly complete innovation cycles.
Contact
Your questions on how to optimize production with automotive additive manufacturing technologies are a priority for voxeljet – get in touch with us today to find out more.
3D Printing Solutions
Would you like to learn more about us and 3D printing? Click here for the entire voxeljet solution portfolio.