Mission M
Full-automation
Industrialization of Core Printing (ICP)
Pioneers of the industrialization of core printing and additive series production
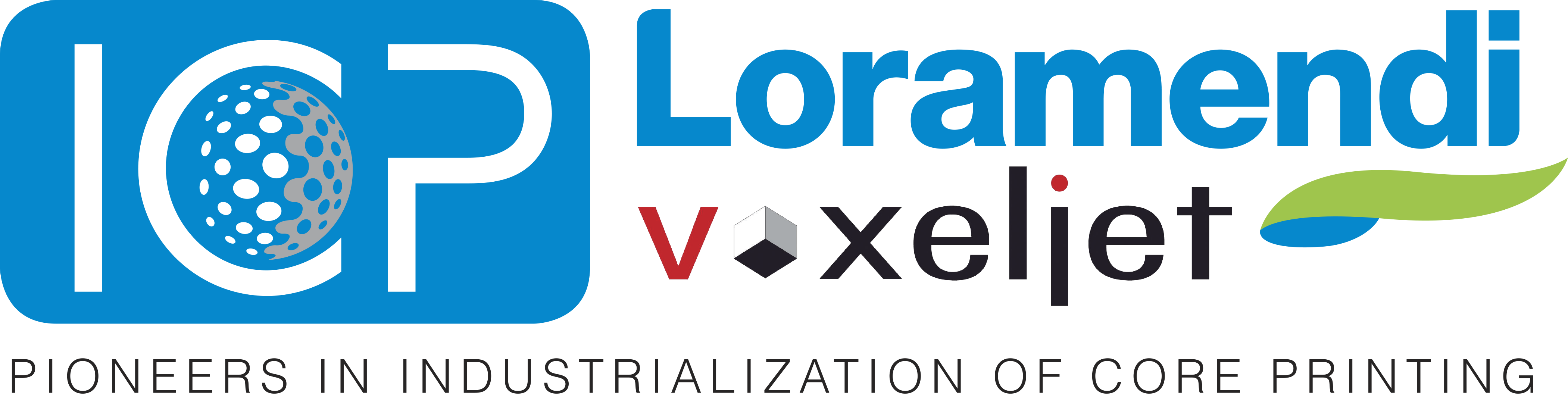
As part of the Industrialization of Core Printing (ICP) cooperation project, we installed and commissioned the world’s first fully automated additive manufacturing cell together with Loramendi, a Spanish expert in foundry equipment.
Installed in the light metal foundry of BMW Group Plant Landshut, Germany, the cell produces several thousand water jacket – outlet combi cores per month for the cylinder head cooling of BMW’s B48 engines. It is the first additive series production solution of its kind and a beacon for all subsequent projects. We are particularly proud of our VX1300X – one of our most powerful printing systems.
Less investment
Layer-based 3D printing eliminates the need for tooling altogether. No long delivery times, no high costs. Full automation limits human intervention to a minimum.
Flexible "tool change"
The elimination of tools also means that a new core geometry can be produced additively at the push of a button without any setup time. For example, today a 4-cylinder water jacket - outlet combi core, tomorrow a 6-cylinder.
Geometric freedom
New, optimized and highly complex designs can be easily manufactured additively. Undercuts are negligible and help revive products thought dead and extend life cycles.
For more than 50 years Loramendi has been developing equipment for the foundry industry and today enjoys a worldwide prestige. We are very excited about this new path, which will completely change the landscape of the foundry industry and set new standards for core making.
Joseba Goitia, General ManagerLoramendi
Designed to meet the specific challenges of the foundry industry.
The example of the ICP project shows that by combining state-of-the-art 3D printers with sophisticated automation technology and suitable post-processing processes, flexible manufacturing cells can be created that can produce hundreds of thousands of complex sand cores per year with a high degree of automation. As the complexity of the components increases, this can also be seen as an economical alternative to standard production processes such as core shooting, or new designs emerge that can only be produced via 3D printing.
Overview of the ICP project
The requirements for the ICP project came from the customer, BMW Group Plant Landshut. It involves the production of a water jacket – outlet combi core which, after casting, reproduces the cooling channels on the cylinder head in the engine block.
The design of the core is so complex that, due to their undercutting, they have the cores manufactured exclusively by additive manufacturing. The complex design can increase the efficiency of the engine by up to 30%, as the cooling can be placed closer to the combustion chamber, thus optimizing heat transfer. The high volumes customary in the automotive sector and the cycle time of the system were the biggest challenges here.
Loramendi and voxeljet have taken up this challenge and, with ICP (Industrialization of Core Printing), have presented for the first time a flexible production cell based on printed sand that produces several hundreds of thousands of cores per year in an automated process. In addition, the ICP project uses exclusively inorganic binders, which has a positive impact on environmental and working conditions.
Whitepaper
Discover the current status of additive series production and explore practical examples.
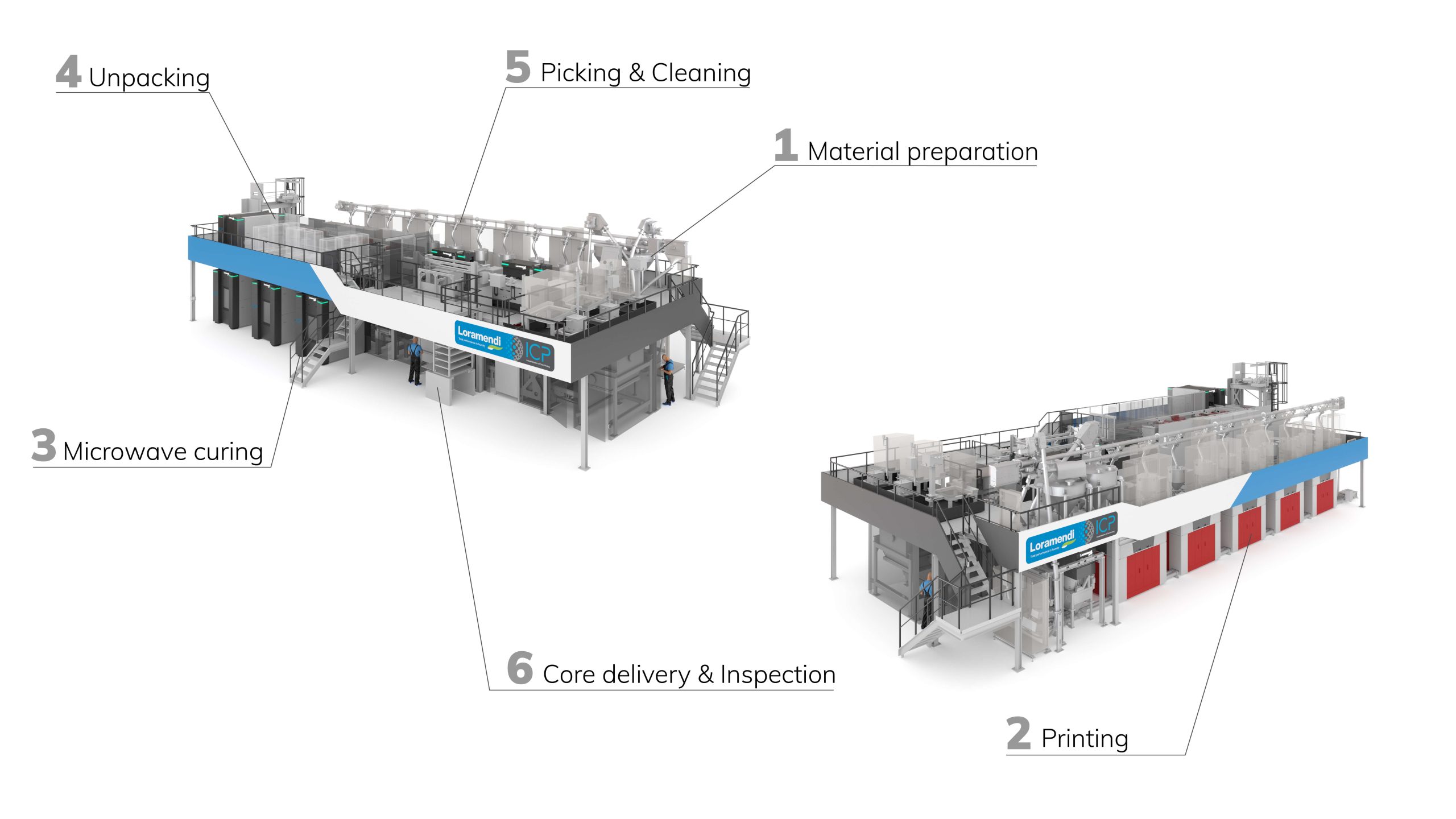
The complete ICP layout
- Material preparation
- Printing
- Microwave curing
- Unpacking
- Picking & Cleaning
- Core delivery & Inspection
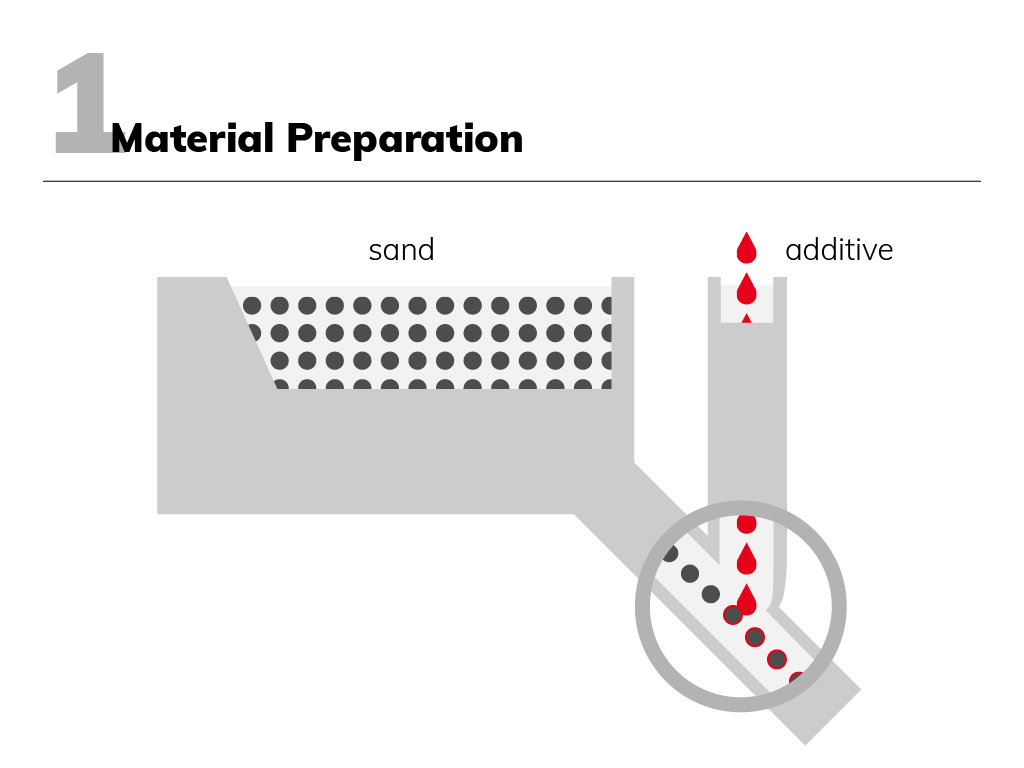
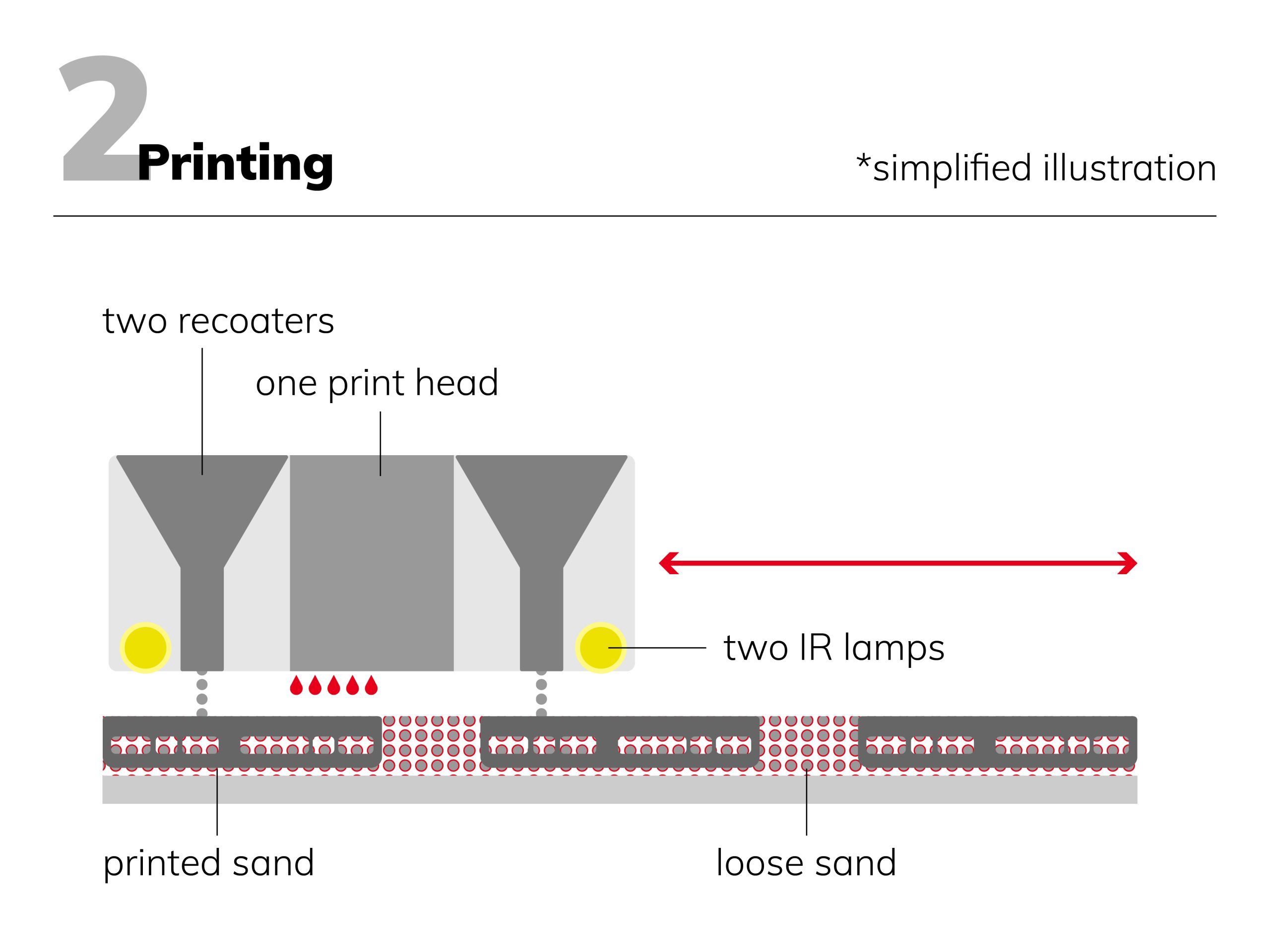
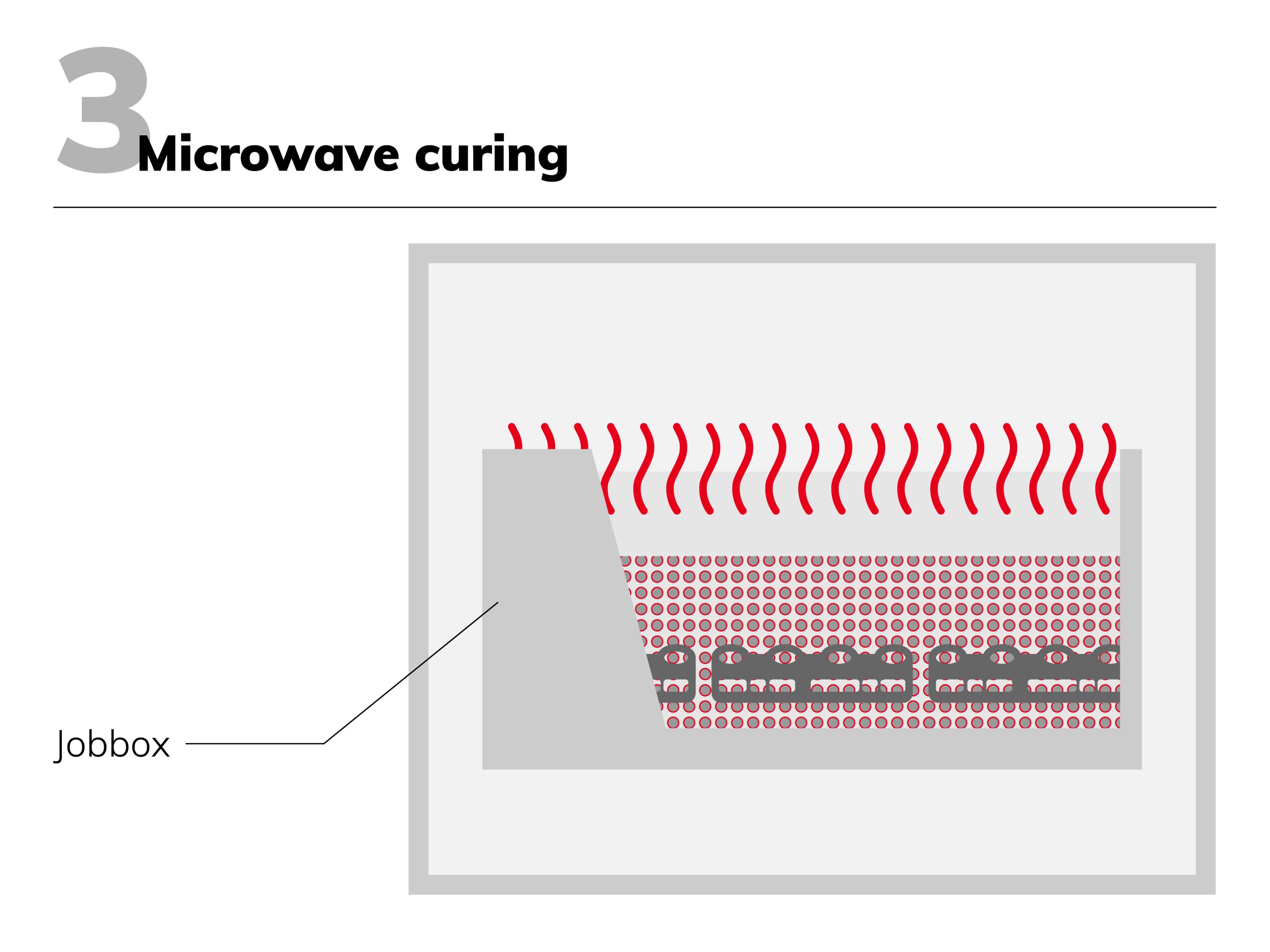
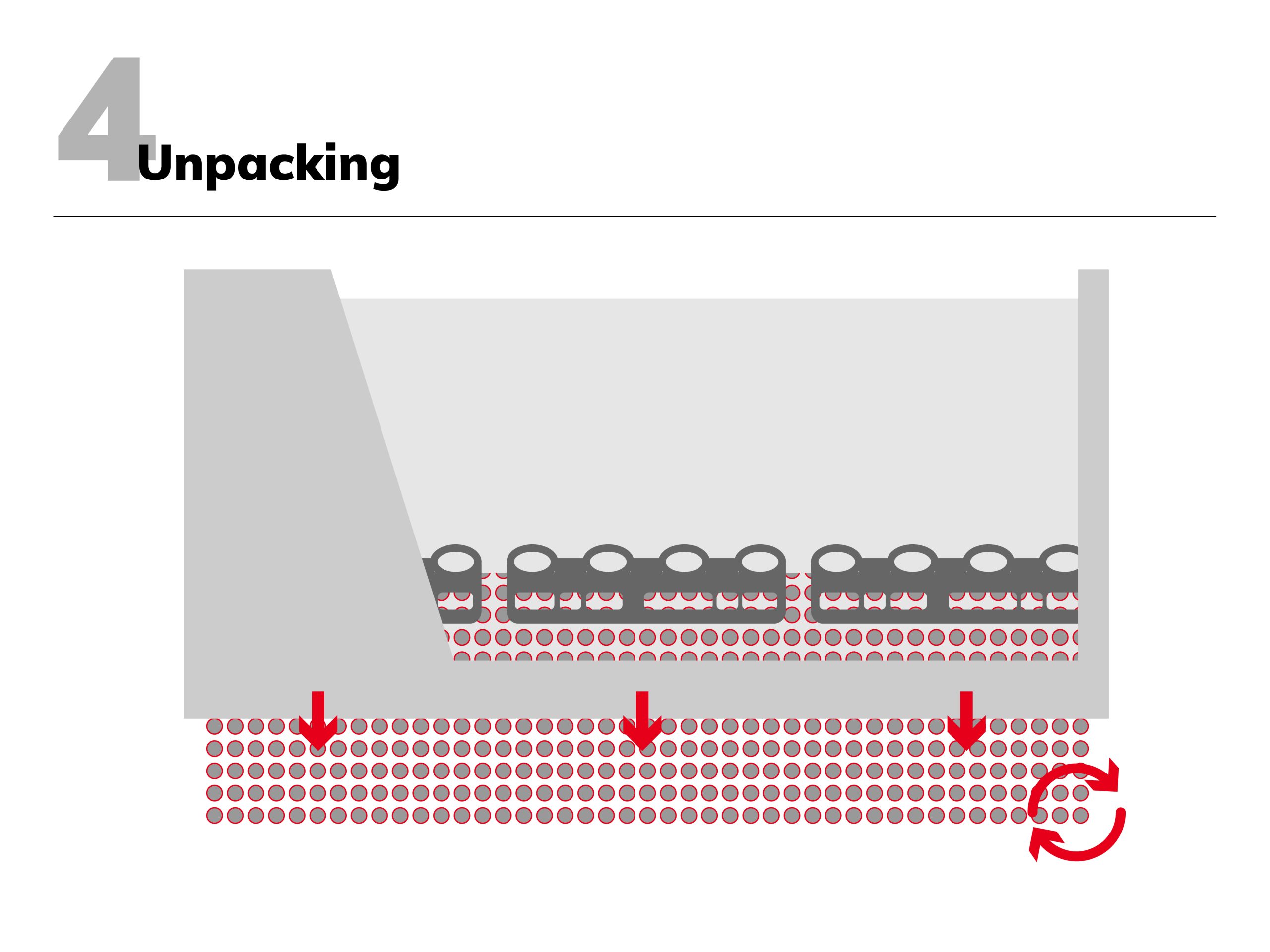
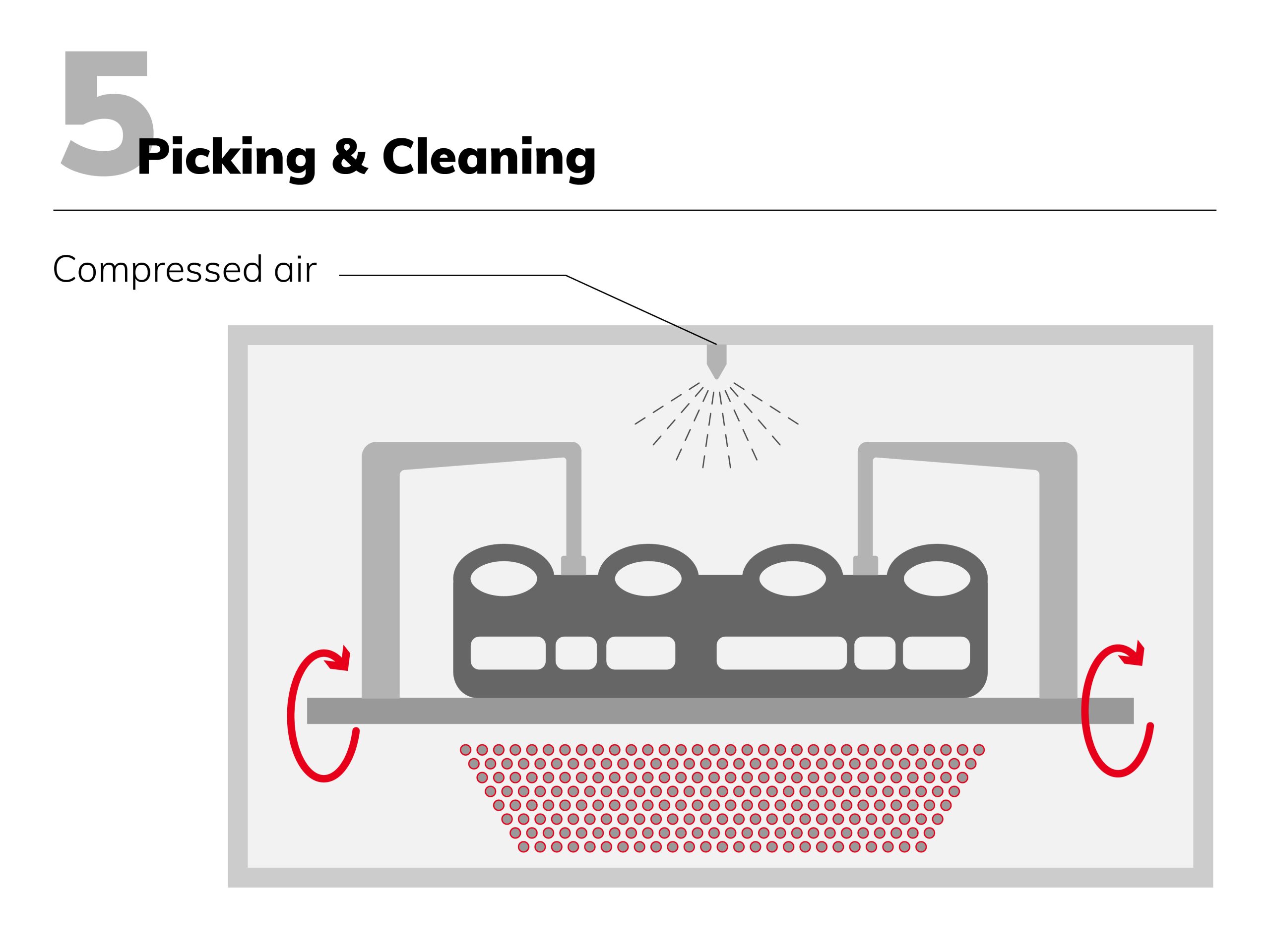

VX1300 X: The revolution of the casting industry
To meet the requirements of additive series production, we have developed a new 3D printer especially for the ICP project: the VX1300X. Equipped with redundant assemblies, predictive maintenance and a unique process unit, it makes a clear statement to standardize 3D printing in series production.
3D printing solutions
Would you like to learn more about us and 3D printing? Click here for the entire voxeljet solution portfolio.