Mission M - Sand
From early beginnings to groundbreaking successes
3D printing of sand for series production
In its early days, 3D printing was used in the foundry industry, particularly for printing models and later for producing molds and cores for prototyping. Over the years, binder jetting in particular became the leading technology due to its scalability in terms of productivity and size.
The potential of the technology was recognized very early on, especially in the aerospace, automotive and energy industries.
However, the road to series production was still long. Apart from the actual printing process, most printers offer few automation options. Work steps such as unpacking and cleaning printed components are mostly carried out manually across all technologies. What makes the process so arduous? And how can these steps be automated? We have the answers:
What does it take to go into production?
At its core, the goal is to increase overall productivity through more productive 3D printers and automation of the unpack/post process in order to reduce unit costs. This requires additive manufacturing not only to adapt the hardware, but also to rethink the design of the entire build process and post-processing:
Optimization of the use of installation space
In the past, it was important to fully utilize the available build volume to optimize 3D printing processes and reduce non-productive times. In the case of binder jetting, this meant placing a large number of components in such a way that as little unprinted sand as possible remained. Depending on the component geometries, a volumetric fill level of 30% can thus be achieved. In the context of automated unpacking, however, it is advisable to arrange components only in one layer so that the loose sand can flow off and the parts are exposed undamaged. In order to maintain overall machine productivity, print rates must be increased and non-productive times further reduced, for example through automated job box replacement.
Hardware customization
Special 3D printing systems are needed for additive series production. Larger build volumes increase productivity, but make it more difficult to access the components. To ensure higher machine availability, several smaller printers are better suited. Our VX1300 X has a medium build volume of 1300 x 650 x 500 mm (390 liters). With a new process unit consisting of a print head that prints the entire build area in one pass and two recoaters, the printer can apply and print a layer in five seconds. In a box with six water jacket cores, less than six minutes are thus required per core.
Complementary solutions
Depending on the construction material used, various finishing stations are required and connected to the printer. When using sand-based materials with an inorganic binder, for example, curing in a microwave oven is required. This is followed by removal of residual sand in a rapid desanding station, followed by a robotic cell for removal and fine desanding. Before storage, the printed components are checked for quality and dimensional accuracy using optical scanners.
Recycling
Last but not least, media supply, in particular sand supply, is a key aspect for the economic efficiency and sustainability of an automated sand printing solution. Existing solutions, such as the ICP project, return unprinted sand from rapid desanding to the cycle, thus reducing the amount of waste and significantly increasing overall cost-efficiency.
Case Studies
So it is not a “plug-and-play” solution. In the context of additive series production, it is essential to rigorously evaluate the individual goals, requirements and resources and to adapt the solution accordingly. Only then can fully automated, additive series production succeed. However, there are also other ways and degrees of automation.
Take a look at our case studies below. From fully automated additive series production at BMW in Landshut, to additive production in the USA, to mass production on demand from our service centers.
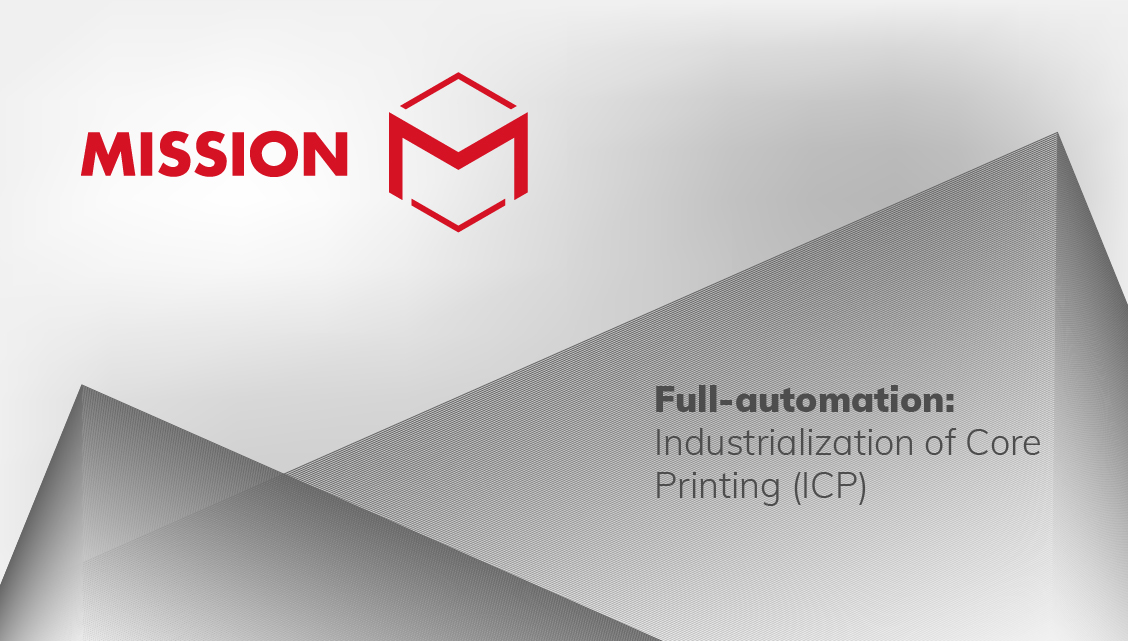
Full automation
From start to finish – here, humans are only used in the rarest of cases. The BMW Group is already implementing this option at its foundry in Landshut:
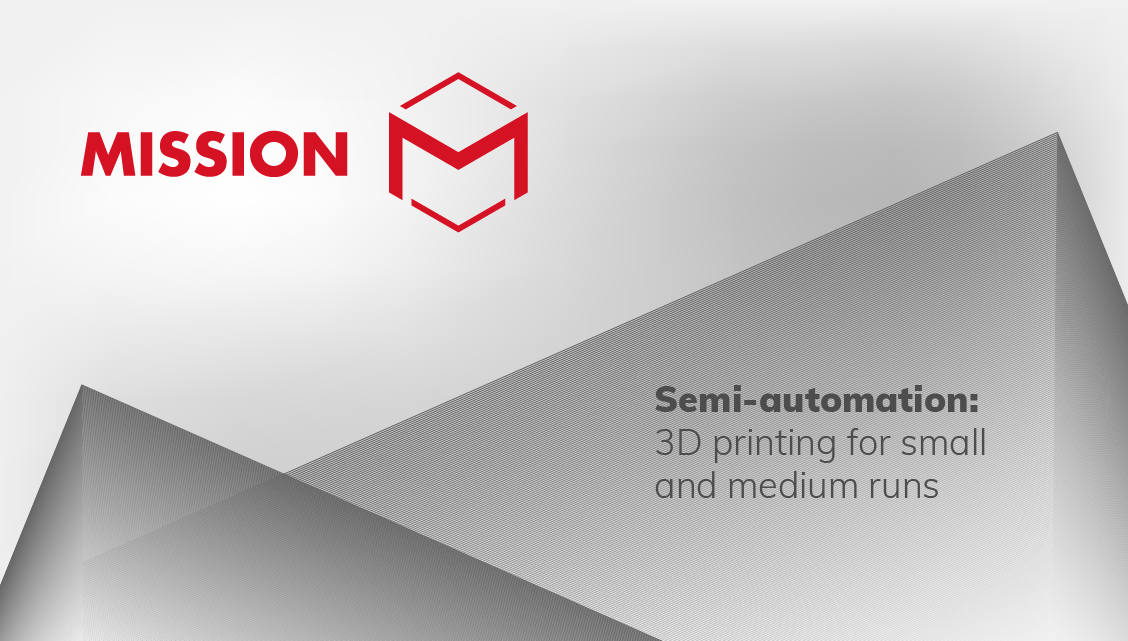
Semi-automation
Smart engineering and semi-automated additive manufacturing enables adaptable production of volume components. This US foundry and Cadillac are setting a new benchmark in giga-castings:
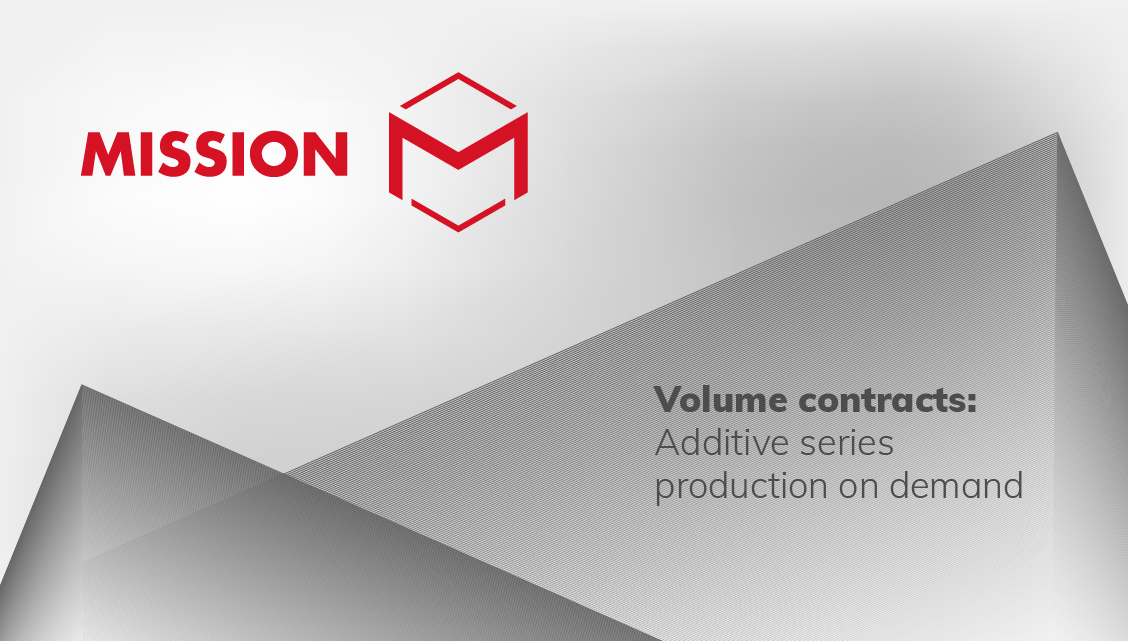
Volume contracts
Even without an in-house 3D printing system, components can be manufactured additively and in series. A fixed callable volume ensures the provision of molds and models on demand.
3D printing solutions
Would you like to learn more about us and 3D printing? Click here for the entire voxeljet solution portfolio.